CANUNDA-HP: a standard configuration with multiple possibilities?
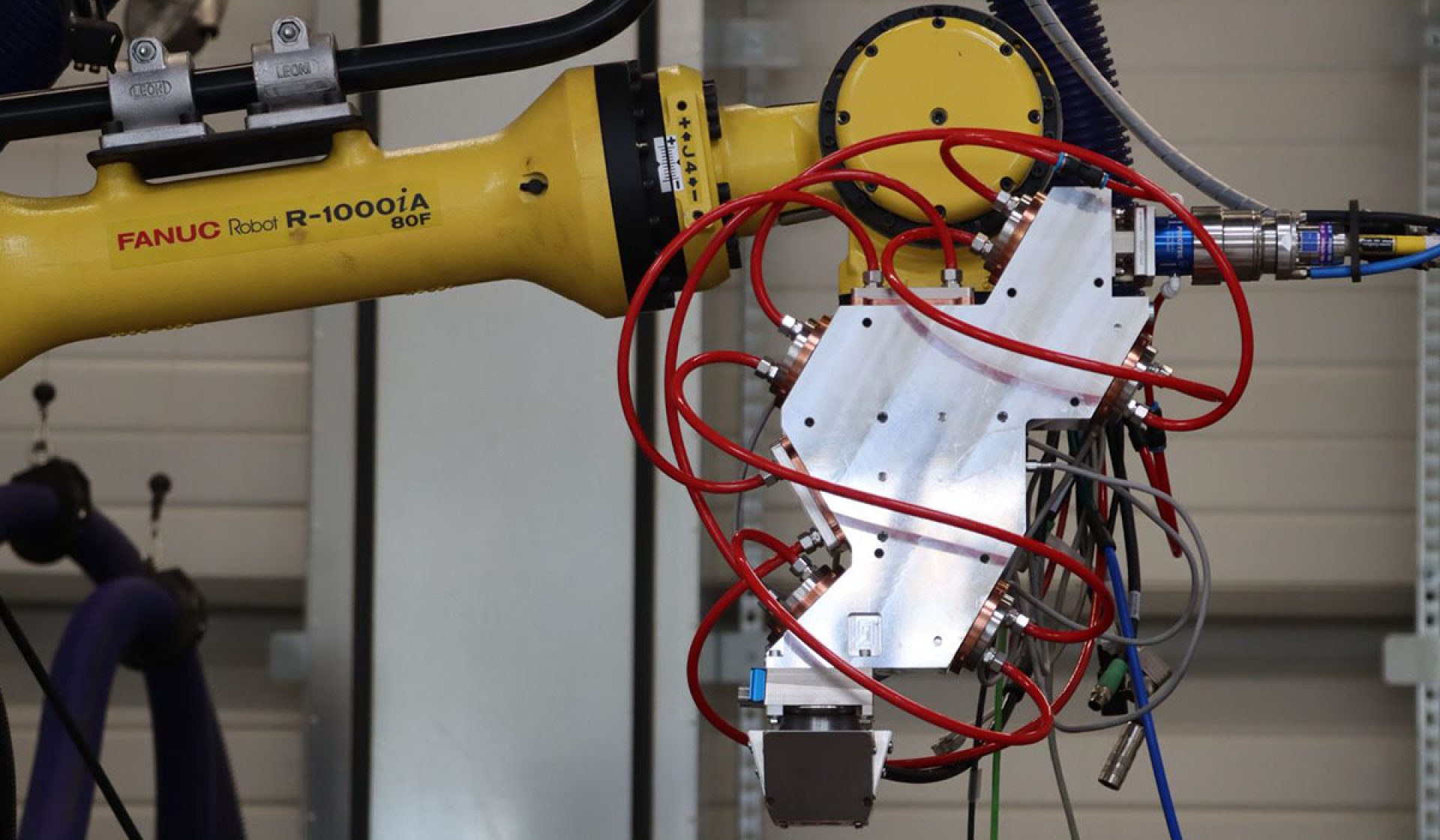
The CANUNDA-HP laser welding head has demonstrated its benefits under design operating conditions: beam quality, robustness, ease of integration, etc. But what happens when you push the system outside its comfort zone? At Cailabs, we wanted to see how CANUNDA-HP would react when the laser source does not comply with the recommended specifications.
We also wanted to show that it is possible to change the size of the ring to meet various industrial needs by making minor adjustments to the standard product. In this article, we will present the results of the tests and numerical simulations conducted here at Cailabs.
Note: This is the fourth and last article in a series dedicated to laser welding processes.
If you change the laser, the shape obtained stays the same
The operating conditions determine the shape obtained
The CANUNDA-HP module forms a ring with an average diameter of 800 µm and a thickness of 200 µm when used under its design operating conditions. These conditions are defined by a laser source with specific properties:
- Power: 16 kW
- Wavelength: 1030 nm
- Numerical Aperture: 0.10
- BPP (Beam Parameter Product): 8 mm.rad
- Input fiber diameter: 200 µm
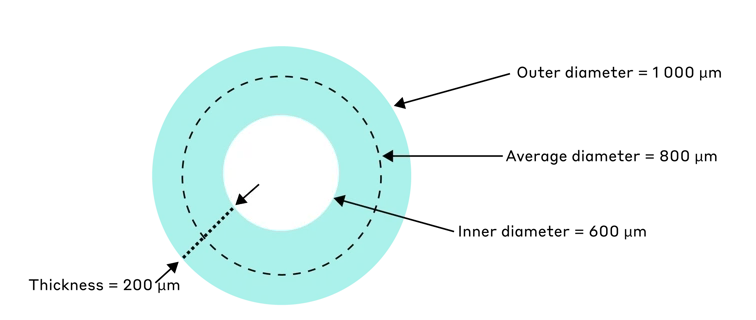
For the purposes of our study, we took the ring diameter as the average diameter of the circle, defined by the maximum intensity along the ring, and the ring thickness as the full width of the ring at half maximum.
These source properties are actually those of a specific laser: the TRUMPF TruDisk 16002. So, what happens when you connect another laser source to the module?
Certain parameters, such as numerical aperture, the diameter of the input fiber and the Beam Parameter Product (BPP) can have a significant impact on the behavior of the optical system. These parameters are defined by the type of laser source and vary from one model to another. Our aim was to estimate the impact of these parameters on our system, so we selected two lasers commonly used in the industry:
Trumpf TruDisk 8001:
- Disk laser
- Power: 8 kW
- Wavelength: 1030 nm
- Numerical aperture: 0.10
- BPP (Beam Parameter Product): 4 mm.rad
- Input fiber diameter: 100 µm
Coherent-Rofin HighLight FL8000:
- Fiber laser
- Power: 8 kW
- Wavelength: 1070 nm
- Numerical aperture: 0.2
- BPP (Beam Parameter Product): 3.3 mm.rad
- Input fiber diameter: 100 µm
Simulation results
First, we performed computer simulations using a Python program developed by Cailabs. They took into account the modal content of the selected laser sources, the diameter and numerical aperture of the input fiber, and estimated the beam shape that would be obtained with CANUNDA-HP.
The benchmark was set by simulating using the design operating parameters, corresponding to those of the Trumpf TruDisk 16002 laser. The ring obtained by simulation was equivalent to that obtained during the tests conducted at the Institut Maupertuis.
Trumpf TruDisk 16002 (benchmark) |
![]() |
Average ring diameter: 800 µmRing thickness: 200 µm |
We then performed the simulations for the TruDisk 8001 and Rofin FL8000 lasers.
Trumpf TruDisk 8001 | Coherent-Rofin HighLight FL8000 |
![]() | ![]() |
Average ring diameter: 800 µm Ring thickness: 150 µm | Average ring diameter: 800 µm Ring thickness: 130 µm |
First of all, we observed that the beam shape remained constant: we always obtain a ring. We also observed changes in size: the average diameter of the ring remained the same (close to 800 µm) but its thickness varied slightly, from 150 µm with the TruDisk 8001 to 130 µm with the Rofin FL8000.
Test results
We designed a test to evaluate the impact a change of fiber would have on the system in order to complete these simulation results. To do this, we used an internally developed high-power connector, which allows fibers with different numerical apertures and diameters to connect to a standard CANUNDA-HP module.
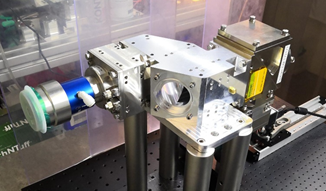
We used two low-power, step-index profile fibers with the following characteristics: diameter of 200 µm and numerical aperture of 0.1 and 0.2. In both cases, the shape and diameter of the ring were preserved, although slightly wider. To confirm the simulation results, we connected a final fiber: the one corresponding to the Rofin laser with a numerical aperture of 0.2 and a diameter of 100 µm.
These tests therefore allowed us to demonstrate that it is possible to go beyond the design operating conditions of numerical aperture and core diameter and still obtain good beam-shaping performance.
Adapting the CANUNDA-HP head to all requirements
In addition to its nominal configuration, which has proven its performance for welding with a Trudisk 16002 laser, the CANUNDA-HP ring shaper can be used with other sources, like the TruDisk 8001 or the Rofin FL8000.
But what about lasers with less comparable characteristics, such as IPG or Laserline lasers? The standard module cannot necessarily meet all the needs of the industry. So, what are the customization possibilities of the CANUNDA-HP head?
- You can adapt the head to lasers with less comparable properties. For use with a laser with a higher numerical aperture (up to 0.2), you can modify the collimation optics or adapt the system dimensions to allow the beam to be transmitted without loss of power.
- You can generate rings of various sizes to suit the materials to be welded, or for different sheet thicknesses. For example, you can redesign the head to obtain smaller (300 µm diameter, 100 µm thickness) or larger (1 mm diameter, 200 µm thickness) rings.
- You can also modify the head’s last optic, which creates the beam’s focus, to suit different working distances, up to 300 mm.
- The shaping optics can also be modified to generate other patterns on demand, such as an intense spot surrounded by a ring, typically used for copper welding, or asymmetric shapes for cutting.
- Finally, multiple accessories can be fitted to the head via the interfaces provided for this purpose, such as laser pointers for positioning. Cailabs has developed its axis camera to allow the head to be adjusted at the beginning of the process, and can also design numerous tools on request, such as coaxial or lateral shield gas.
This article concludes the series on laser welding. First, we looked at conventional techniques in general, then we focused on the laser and the value of beam shaping to boost this process. Then we put forward arguments to demonstrate the relevance of the technology proposed by Cailabs (MPLC) in comparison with other technologies applied to laser welding solutions.
We saw how the CANUNDA-HP module improves the quality and efficiency of processes in an industrial setting. Finally, we saw that this standard solution also opens up the possibilities for more custom requirements and can be adapted to various existing environments.
For more information, please download our CANUNDA-HP brochure.
Watch the webinar replay co-presented by Cailabs and Institut Maupertuis for more detailed application results. New results will be available soon: stay tuned!
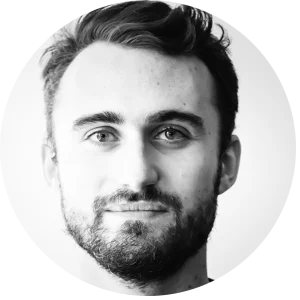
By Julien Bayol
Julien Bayol holds a Master’s degree in mechanics from INSA and has completed a Master’s degree in Management at Toulouse Business School. Very interested in advanced manufacturing techniques, through the use of innovative optical solutions, Julien is assistant product manager at Cailabs. He contributes to the development and commercialization of CANUNDA and TILBA® products.
Our Other Articles:
-
Exceeding Throughput Limits with Laser Communications
-
The challenges of e-mobility: Welding busbars
-
Flying further with beam shaping
-
From the Volkswagen Golf to the Tesla Model 3: How Lasers Are Shaping the Automotive Industry?
-
Space Optical Communications: Why Are Space-to-ground Links Taking Time to Develop?