From the Volkswagen Golf to the Tesla Model 3: How Lasers Are Shaping the Automotive Industry?
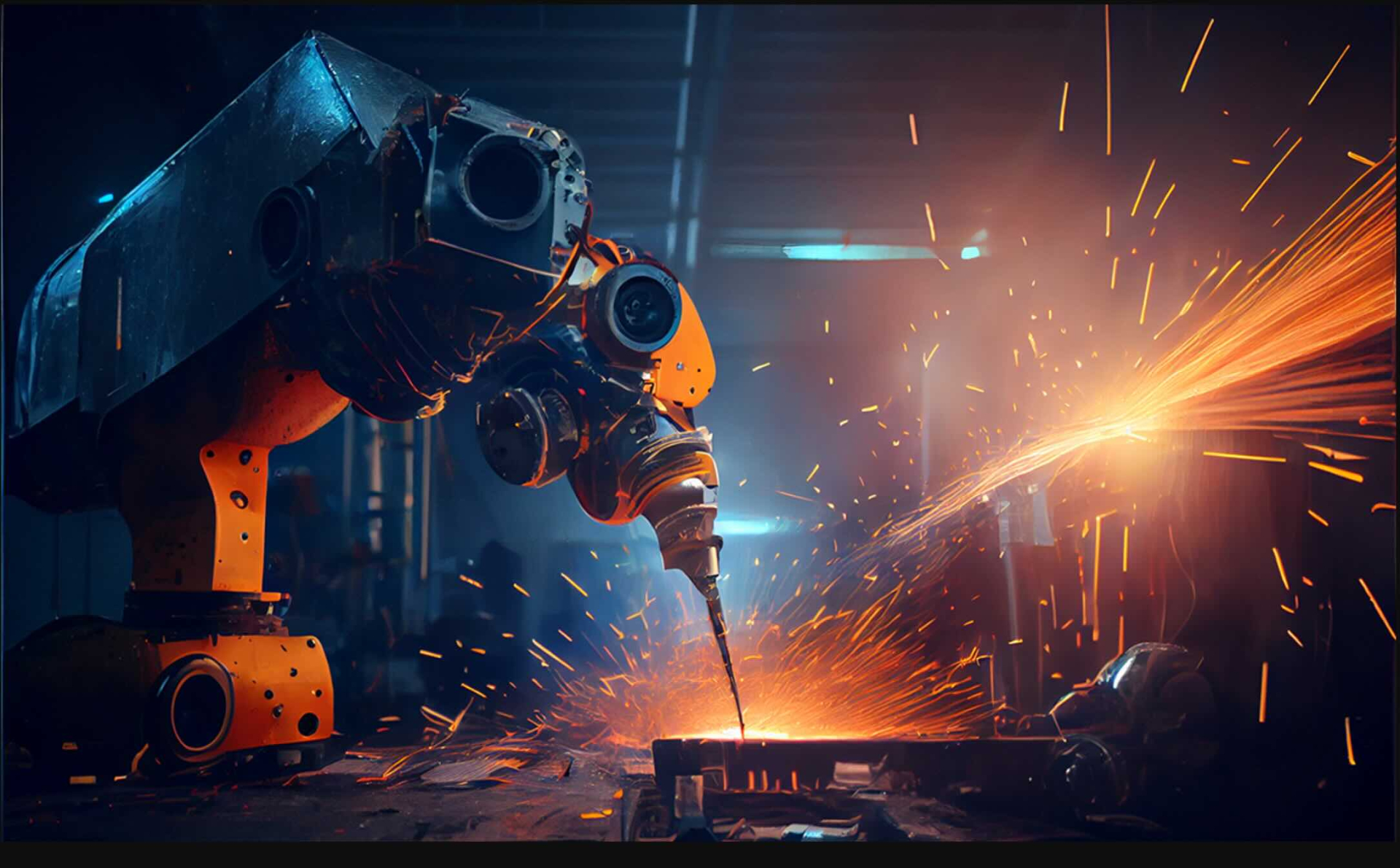
Electromobility, or e-mobility, is revolutionizing the automotive industry and emerging as a priority for automakers worldwide. Laser technology has become a key element in meeting the challenges of mass production of electric vehicles (EV).
Note: This article is the first in a series on lasers in e-mobility
The history of the automobile:
The earliest automobiles date back to the 19th century, when the first steam-powered vehicles were built. However, it wasn’t until the late 1800s that cars became more convenient with the invention of the internal combustion engine. The first models were expensive and only the wealthy could afford them. In 1908, Henry Ford started mass producing the Ford T and invented the first automobile that was accessible to the general public.
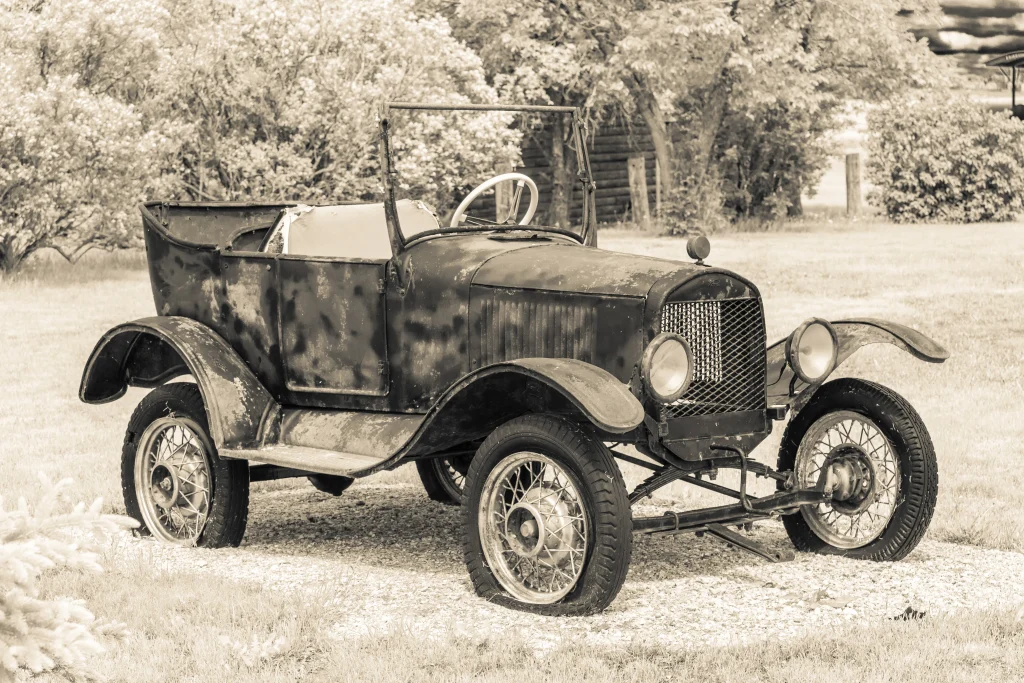
In the 20th century, the automotive industry grew rapidly, with the emergence of new technology, brands and models. Cars also began to play an increasingly important role in society, with significant changes in lifestyle, urbanization and infrastructure.
Over the years, cars have evolved to become safer, greener and smarter, with advanced driver assistance systems and onboard communication technology. Today, the automotive industry is a key pillar of the global economy, with millions of cars sold worldwide every year.
The adaptability of the automotive industry will once again be of strategic importance to society over the next few decades as we face the challenge of achieving carbon neutrality by 2050 – a necessary requirement if we are to limit global warming to 1.5°C. Transportation accounts for 29% of greenhouse gas emissions worldwide, 54% of which are generated by passenger cars.
Automakers are therefore seeking new, more environmentally friendly energy solutions. Internal combustion engine vehicles are increasingly being replaced by electric or hybrid vehicles. However, many environmental, industrial and political challenges still need to be met for this to become a viable long-term solution. In addition, the future of the automotive industry could veer towards hydrogen-powered cars, which are just starting to emerge.
The origin of e-mobility
The origins of e-mobility dates back to the 19th century.
- In 1830, the first electric vehicle prototype was created.
- In 1881, the first viable electric car was developed by three Frenchmen: Camille Faure, an electrochemist who was working on improving the design of lead batteries; Charles Jeantaud, a car manufacturer; and Nicolas Raffard, a mechanical engineer.
At that time, electric cars were popular with the upper classes because they were quiet and emission-free.
In the early 1900s, the arrival of Ford and the mass production of gas-powered cars made e-mobility less attractive. Inexpensive, more powerful and accessible, internal combustion engine cars monopolized the market throughout the 20th century.
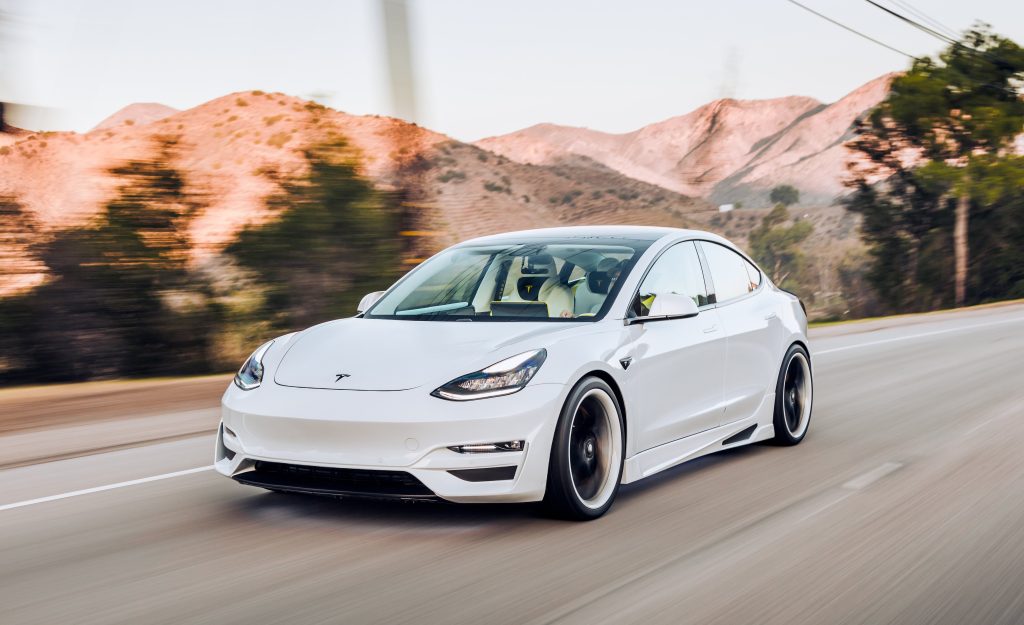
E-mobility has had its ups and downs over the years. In the 1970s, the oil crisis brought about a renewed interest in electric cars. However, battery limitations hindered their development.
It wasn’t until the 2000s that e-mobility experienced a revival, thanks to improved lithium-ion batteries and rising oil prices. E-mobility is now becoming a viable and attractive alternative to gas-powered cars. Tesla has played a key role in the development of electric vehicles, popularizing the technology and showing that they can rival gas-powered cars in both performance and range. The number of electric vehicles has grown steadily since 2010, with many of the world’s leading car manufacturers taking up the challenge.
The e-mobility market
With the political environment supporting the ecological transition, the e-mobility market is currently enjoying very strong growth worldwide. Global EV sales exceeded 10 million in 2022, compared with less than 1 million in 2015. According to estimates from the International Energy Agency (IEA), sales should continue to rise, reaching 14 million in 2023, up 35% compared to 2022. By 2030, light electric vehicles (LEV) should account for over 50% of car sales.
This growth is mainly due to increased EV production by automakers. By 2035, all new 4-wheel road vehicles under 3.5 metric tons sold in Europe must have zero CO2 emissions. This agreement, which was validated by the 27 members of the European Union in 2023, is driving automakers worldwide to invest in more efficient battery technologies and develop new EV models to meet growing demand.
Energy companies are also investing in innovative charging solutions to facilitate the transition to e-mobility. Lastly, governments around the world are supporting the transition by offering subsidies and incentives to purchase electric vehicles. Rising oil prices and increasing environmental awareness are also driving consumers toward electric cars.
China currently accounts for nearly 60% of EV sales. Europe and the United States are the second and third biggest markets.
The growing popularity of “all-electric” models has led to increasingly tough competition between manufacturers. If we look at deliveries of 100% electric vehicles worldwide, Tesla retained its position as market leader in 2022 with a share of around 18%. However, the gap with its main competitors is narrowing. In second place, the fast-growing Chinese group BYD has a share of around 13%. Year-on-year, Tesla lost 3% of market share, while BYD gained 4%. If these trends continue, analysts predict that BYD could overtake Tesla around the third quarter of 2023.
Despite this, the automotive industry is currently facing a major problem: Increased demand has created a shortage of lithium, an essential component of batteries. The price of lithium increased by over 500% in 2022, creating considerable tension in the automotive industry. While today there is no mobility without oil, tomorrow there will be no mobility without batteries. Currently, Asia (China, South Korea and Japan) enjoys a virtual monopoly on their manufacture. It is therefore in the interest of European and US automakers to develop their own batteries to face this competition from Asia. The number of battery manufacturing facilities in Europe and the US should therefore increase significantly over the next few years.
The history of lasers in the automotive industry
Volvo was the first automaker to use laser technology in its manufacturing processes, but Volkswagen was the company that really popularized this practice. In the early 1990s, the TRUMPF Group began using lasers to weld automotive sheet metal, and today is the world leader in this application. In 2003, the Volkswagen Group already had more than 450 lasers in operation at several plants worldwide. Lasers are used to weld a variety of body parts, including vehicle frames, doors, roofs, hoods, pillars and trunk lids. This technology enables faster, more precise welding, particularly of zinc-coated sheet steel, and has become a standard in the modern automotive industry.
The automotive industry is one of the biggest users of laser technology. There are many significant advantages to using laser in this field:
- High precision: Modern lasers are extremely precise and deliver high-quality results, even on parts with significant positional variations. Vision cameras and special optical configurations reduce errors and ensure consistent quality.
- Practical changes: System changes are executed quickly and can be fully automated using specific software.
- High processing speed: Lasers have a high processing speed, which increases productivity for automakers.
- Waste reduction: Lasers operate without consumables, considerably reducing waste, which is further reduced by the lack of tool wear and tear.
- Suitable for small manufacturing spaces: Laser machines are now more compact and can operate efficiently in confined spaces.
- Flexibility: Lasers are versatile and can be used in a variety of processes, including cleaning, drilling, welding, engraving and marking. Laser parameters can also be changed at any time, allowing multiple operations to be performed. Lasers can also handle complex surfaces and geometries that are difficult to process with standard tools.
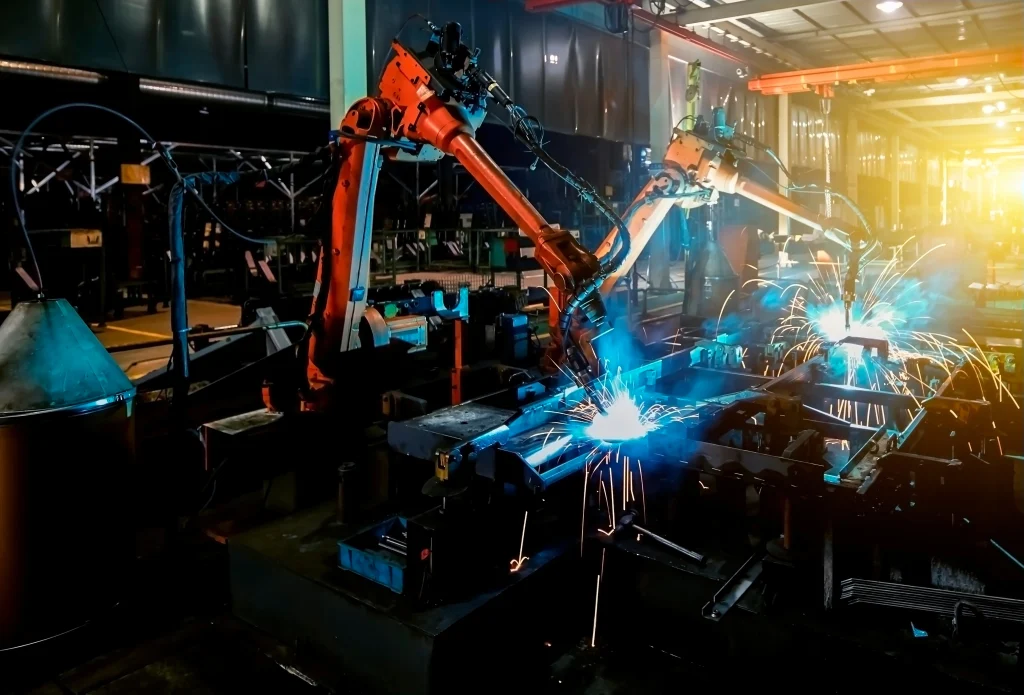
There are many applications for laser technology in the automotive industry. For example, they are used to drill holes, cut materials, and engrave and treat surfaces. However, laser welding remains a widespread application.
The growing use of lightweight parts to improve vehicle performance has also favored the use of lasers, as these materials (plastics, aluminum, etc.) are often more difficult to machine (deformations, defects, loss of properties, etc.).
E-mobility: New requirements
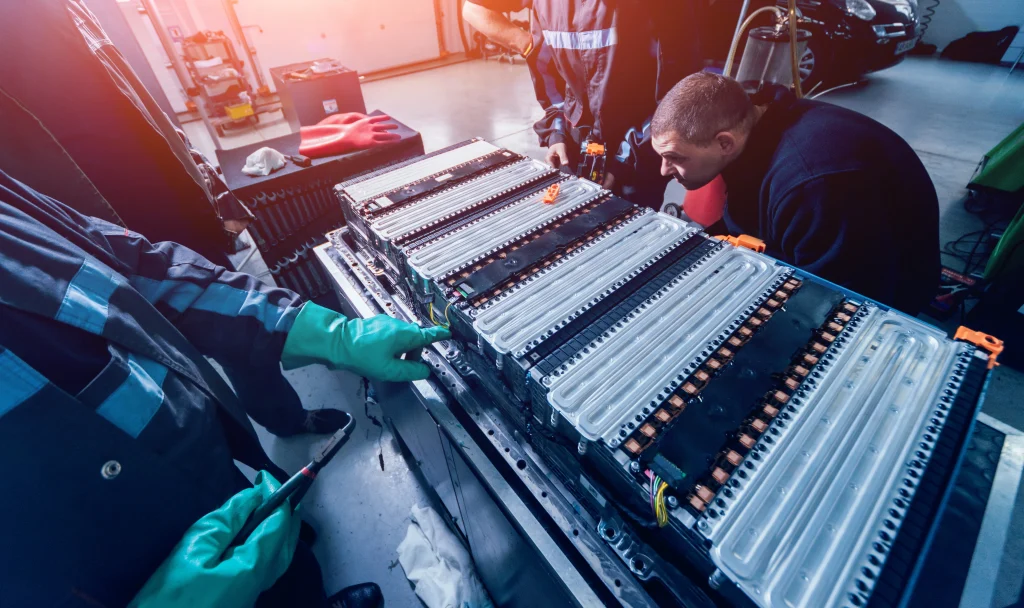
These new trends have intensified with the democratization of electric vehicles. The automotive manufacturing process needs numerous improvements to meet these new requirements. Vehicle performance is a priority issue, and engineers are continuously working to improve battery range, charging and performance to attract as many consumers as possible to e-mobility.
Vehicles are also becoming increasingly complex and technical. Electric vehicles have very high manufacturing costs, which have a knock-on effect on sales prices. Manufacturers therefore need to optimize their manufacturing methods and identify new, more efficient industrialization processes to meet tomorrow’s challenges.
In particular, the need for copper and aluminum welding has exploded with this new trend. Copper is used as an electrical conductor, while aluminum is used to compensate for the significant weight of vehicle batteries, and for its heat-conducting properties. Welding these two materials is still a challenging task, so suitable solutions will need to be developed over the coming years. Part of the solution lies in laser technologies that can improve welding, cutting and surface treatment processes.
More specifically, light shaping makes it possible to optimize the shape of laser beams to suit different requirements and increase performance. Cailabs’ CANUNDA product line does just that. For example, Cailabs offers a beam shaping module that can generate a very intense spot surrounded by a ring, which is ideal for infrared copper welding.
In the following articles, we will focus on the main laser processes that can be improved using Cailabs’ CANUNDA product line.
References :
(1) Lasers in the automotive industry, what you need to know – baba-blog.com . Read the article
(2) Le laser, histoire d’une découverte lumineuse – CNRS Le Journal. Read the article
(3) Les avantages du laser dans l’industrie automobile – Sociétés Industrie. Read the article
(4) L’histoire de la machine de découpe laser – Outillage industriel. Read the article
(5) Les ventes de véhicules électriques dans le monde vont s’envoler en 2023, selon les prévisions de l’AIE – L’Usine Nouvelle . Read the article
(6) Fin des moteurs thermiques en 2035 : que contient l’accord, quelles voitures pourront encore rouler après cette date ? – Midi Libre . Read the article
(7) Histoire de la voiture électrique : une évolution impressionnante ! – BEQ Technology. Read the article
(8) Voitures électriques : les constructeurs chinois montent en puissance – Statista . Read the article
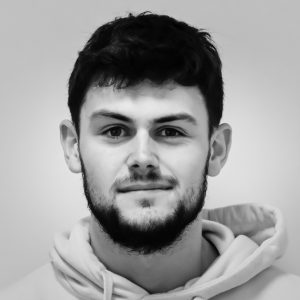
By Adrien Douard
Currently a student engineer specializing in industrial engineering at ECAM Rennes, Adrien Douard completed a year of Operations Management at ESSCA in Angers. Particularly interested in the automotive industry and its processes, Adrien is assistant product manager at Cailabs. He contributes to the development and commercialization of CANUNDA products, that optimize the quality and performance of laser based machining processes.