Glass cutting using bessel beams
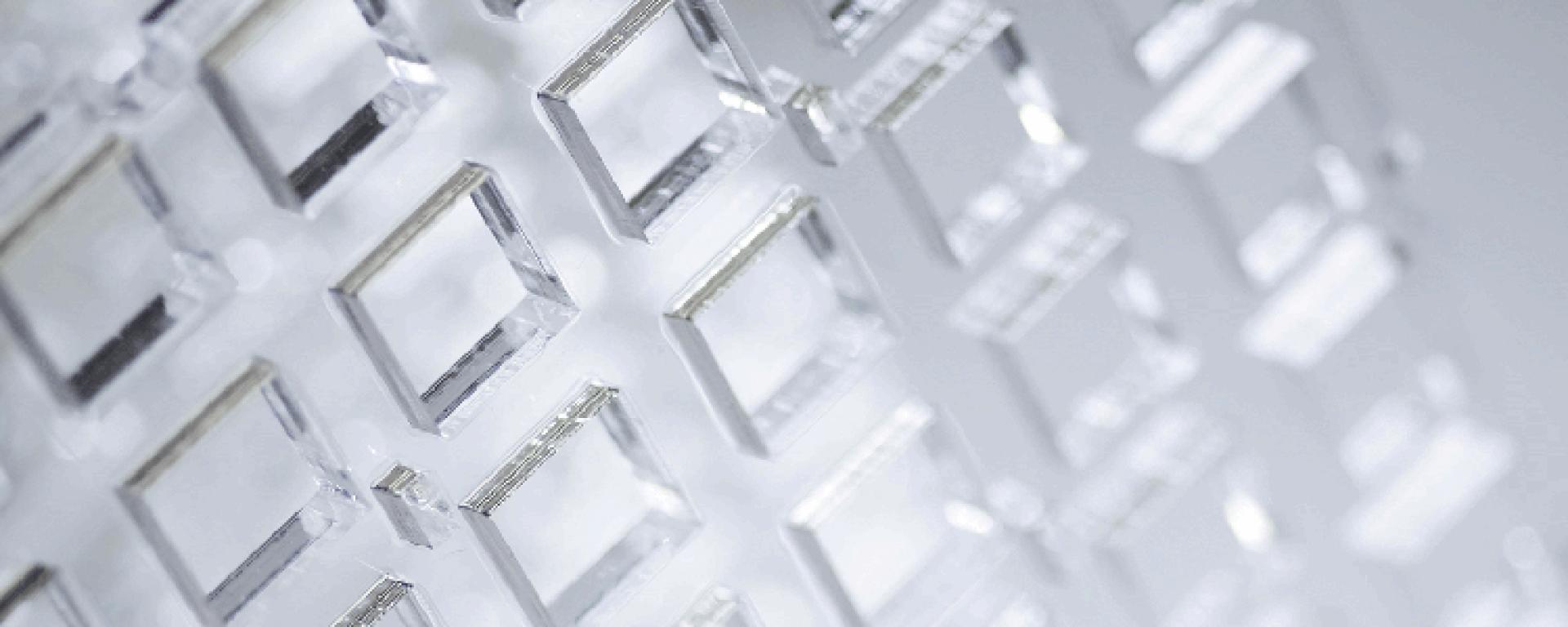
Glass machining processes that are highly efficient, highly accurate and low cost are becoming increasingly popular in the industry, especiallyfor the manufacturing of LEDs, display screens and watch glasses [1].
Ultrashort-pulse lasers (USP lasers) represent an important advance in the realm of glass machining tools because they allow, unlike mechanical manufacturing or with more conventional lasers, to process transparent and fragile materials while minimizing as much as possible the thermal effects generally responsible for alterations to the mechanical and optical properties [2].
However, their limited average power decreases their efficiency, making it all the more necessary to make the best possible use out of interactions of ultra-short laser pulses with manufactured glass in order to increase the machining speeds. Laser beam shaping using Bessel beams is proving to be a highly advantageous solution in the domain of glass manufacturing.
Bessel Beams
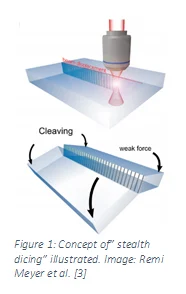
There are several ultrafast laser glass machining processes, but today the technique with the highest cutting efficiency is known as stealth dicing [3]. This process consists of scanning the beam and drilling channels in the material along intended cutting lines according to the desired shape, then applying an external mechanical force to induce a controlled fracture that will propagate along this shape (Fig. 1) [3]. The speed of this method, allowing machining speeds of up to several meters per second, results from the high drilling rates that can be achieved with certain types of ultra-short lasers (up to several hundred thousand holes per second).
The precision and regularity of drilling is essential to obtaining a clean, precise cut with minimal debris. Therefore, it is highly important to be able to precisely control how deep the laser beam propagates into the material. The different conventional drilling methods currently being used, such as simple ablation or filamentation, offer a limited output, have limited accuracy and unpredictable results which prevent them from being applied efficiently and reliably on an industrial scale [3]. Since 2017, the use of laser beam shaping technologies for generating Bessel beams has proven itself as an effective method that responds to this need, allowing for precise drilling control.
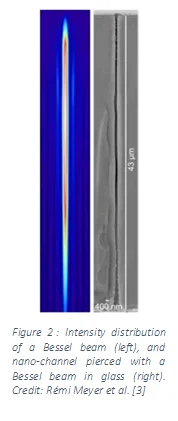
Bessel beams are a type of laser beam created by interference over a long distance, allowing an intense concentration of energy that can propagate without diffraction inside transparent materials (Fig.2). Bessel beams generated with an USP allow a deep ablation of the irradiated material, which is particularly useful for drilling nano-channels with high aspect ratios (fig.2).
It is thus possible to drill into glass layers that are several mm thick with very small diameters (less than 2 micrometers) and having a largely homogeneous shape [3]. The advantage of using Bessel beams for nano-channel drilling is that the shape of the laser beam defines the dimensions of the hole. In controlling the shape of the Bessel beam, it is possible to have more control over drilling.
It is therefore a simpler, more controlled method with better reproducibility compared to the methods that have been used up until now. It distinguishes itself as being the technique with the most control over drilling, with the qualities and machining precision necessary for the micromachining of glass on an industrial scale.
Generating Bessel beams
Several laser beam shaping technologies make it possible to obtain Bessel beams. For example, conical lenses (axicons) and spatial light modulators (SLMs) are frequently used to generate them, but suffer from several limitations: SLMs produce high-quality beams (and are reprogrammable), but have low energy efficiency and cannot withstand high powers. Conic lenses can withstand high powers, but generate lower quality beams due to manufacturing defects.
Recently, the French company Cailabs, a laser beam shaping system manufacturer, was able to generate high-quality Bessel beams using reflective axicons [4]. These axicons, manufactured with a high degree of precision, enabled the generation of high-quality Bessel beams with excellent energy efficiency (higher than 99%), making them compatible with high power laser beams. It is therefore the most suitable solution for the use of Bessel beams on an industrial scale, combining high efficiency with unparalleled precision.
In the future
Quality, high productivity glass machining is an important issue. While the use of Bessel beams constitutes a major breakthrough in manufacturing quality and accuracy, the combination of Bessel beam shaping technology with beam splitting technology would lead to an even greater breakthrough by increasing the number of holes drilled with each laser pulse and thereby, the machining speed.
Cailabs’ Multi Plane Light Conversion (MPLC) technology, which enables the simultaneous generation and shaping of multiple beams in parallel, could yield unparalleled machining speeds in the range of tens of meters per second. On an industrial scale, such machining speeds would drastically increase production, while maintaining optimum quality and lower operating costs.
Listen to the episode:
(1) Annual Laser Market Review & Forecast: Where have all the lasers gone? by Gail Overton, Allen Nogee, David Belforte, and Conard Holton. Read More
(2) Ahead of the Curve – Lasers Enable Superior Glass Cutting for Demanding Applications by Roland Mayerhofer, Coherent. Read More
(3) The Laser User – Spring 2017 . Read More
(4) Pauline Boucher et al., Generation of high conical angle Bessel-Gauss beams with reflective axicons (2017)
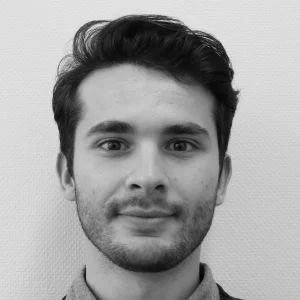
By Sami Laroui
Sami Laroui, who holds Master’s degrees in materials science and innovation and entrepreneurship, joined Cailabs in 2018. As a pre-sales engineer, he contributes to the development and commercialization of innovative optical solutions, that optimize the quality and performance of laser machining processes.
Our Other Articles:
-
Exceeding Throughput Limits with Laser Communications
-
The challenges of e-mobility: Welding busbars
-
Flying further with beam shaping
-
From the Volkswagen Golf to the Tesla Model 3: How Lasers Are Shaping the Automotive Industry?
-
Space Optical Communications: Why Are Space-to-ground Links Taking Time to Develop?