Laser welding: what solutions can respond to industrial challenges?
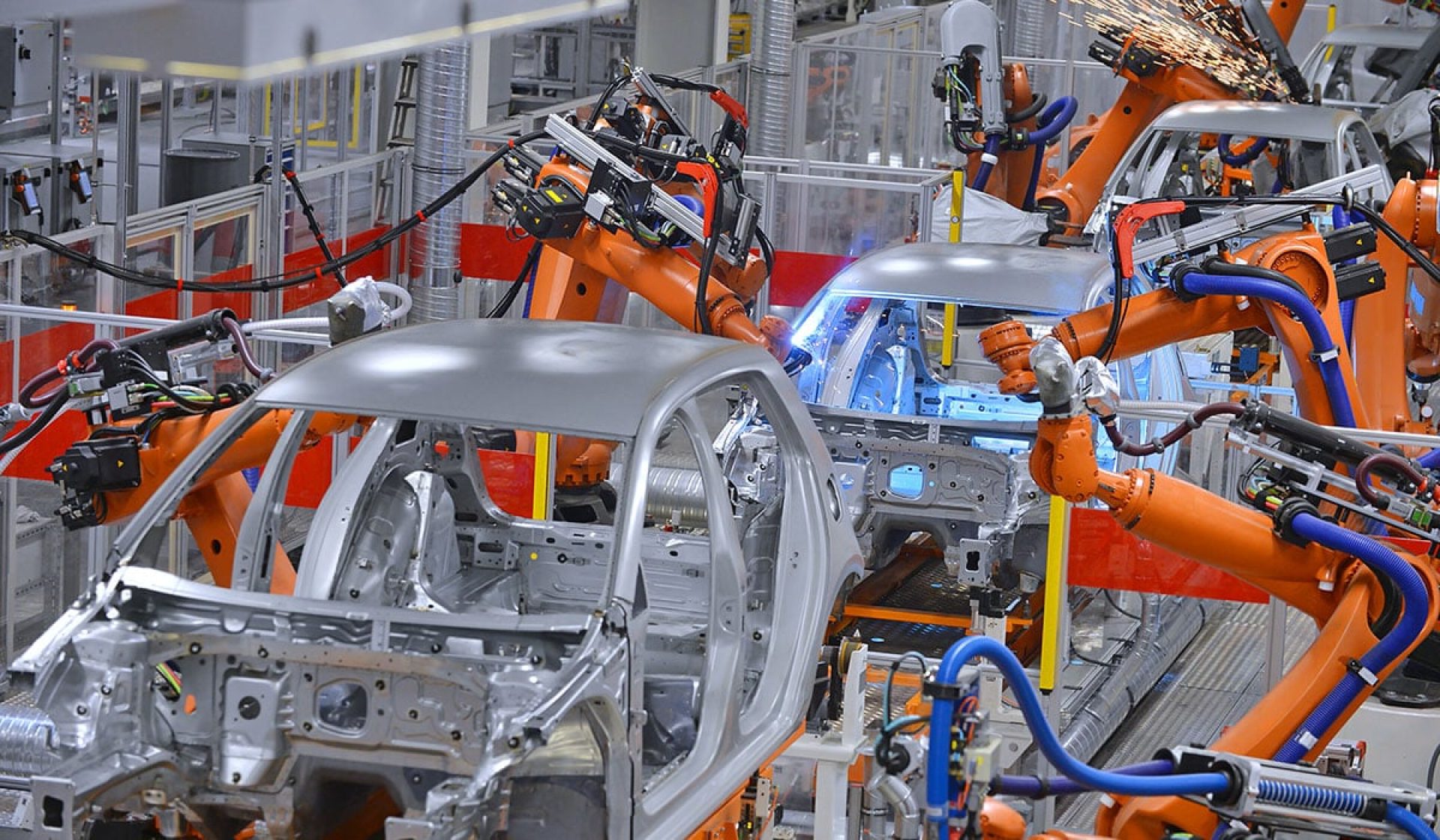
In the first article we looked at conventional welding techniques, now let’s focus on lasers. This technique, which was developed at the end of the 20th century, has many advantages. What are its current applications? What challenges does this technology still face, and with what tools?
Note: this article is the second in a series dedicated to laser welding processes.
How does laser welding work?
In the second half of the 20th century, the use of lasers for welding applications first made an appearance. It was nothing less than a technical revolution. The energy is provided by the laser beam, which is focused on the area to be welded.
This focus makes it possible to achieve very high levels of energy density, i.e. a large amount of energy is concentrated on a small surface. This fully automated technique has many advantages: increased quality and precision, enhanced performance and speed of execution, and good flexibility. It also allows for greater welding depths compared to conventional techniques.(1)
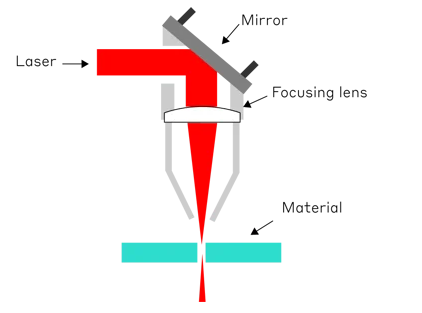
high levels of energy density
There are two different types of laser welding regimes:(2)
- Heat conduction welding: the laser brings the parts to be welded to their melting point, creating a molten pool which flows together and solidifies to form the weld. The parts are only melted by heat conduction, so the weld is not very deep (up to a maximum of one millimeter) and smaller than the weld bead width.
- Deep penetration or keyhole welding: here the energy provided causes the molten pool to boil and the metal therefore begins to vaporize. The vapor creates a vapor-filled hole called a “keyhole”, a kind of bubble which pushes the molten metal to either side. This keyhole moves along the weld at the same speed as the beam and has the effect of amplifying the transmission of the laser energy by reflecting on its walls. This technique makes it possible to achieve much greater welding depths than heat conduction welding.
Since these processes involve large amounts of energy and high-localized temperatures, defects can occur. Some can be seen on a macroscopic scale, while others are much smaller (in the micron range). Standard EN ISO 6520-1 divides these defects into six categories:(3)
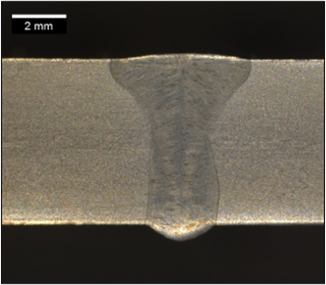
- Crack: local rupture, on a macro or microscopic scale, single or in a network
- Cavity: a blowhole (gas bubble forming in the weld bead); an open blowhole is also known as “pitting”
- Solid inclusions: presence of a solid foreign body in the weld bead
- Lack of fusion and penetration: the metals to be joined have not been fused or welded correctly
- Imperfect shape and dimension: the shape of the external parts or the geometry of the joint is imperfect
- Miscellaneous defects: defects that don’t belong to any of the above categories, for example spatter
A widely-used industrial technique
The annual growth rate of the laser welding machine market is estimated at 5%, with applications in multiple sectors. This technique is especially used in the automotive industry where the manufacturing priorities are large volumes and high-quality standards.
In this sector, laser welding is used to assemble chassis parts, door frames, hoods and trunks, and also more complex sub-parts such as airbag triggers.(4)
In all, the length of weld achieved with this process can be up to 50 meters for a single car! The use of laser sources is expected to increase further in this industry due to the growing interest in e-mobility.
For example, this technique is being developed to weld copper, which is used in particular for electric vehicle batteries. This application is currently rapidly expanding. It has one of the highest growth rates in the laser welding industry.(5)
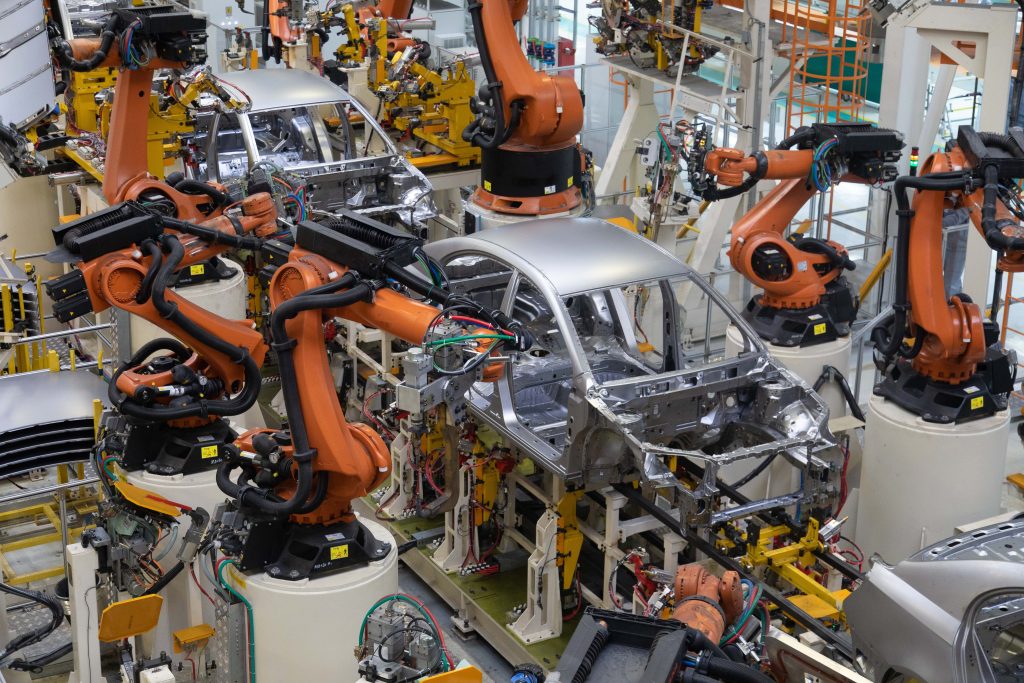
Besides the automotive industry, lasers are used in other industries, such as shipbuilding. Some hybrid laser welding processes are used, like “laser – MIG/MAG welding”, where the weld is made by the combined action of a laser beam and an electric arc with filler metal. This method provides high penetration and high speed over long weld lengths.(6)
Beam shaping to improve laser welding
However, some challenges remain for this process. For example, there are two possible methods for copper welding, each with its respective challenges. The light absorption of copper is wavelength sensitive and varies according to its state: in the solid state, it is high in the green and blue wavelengths, and low in the infrared, but it increases and becomes wavelength insensitive in the liquid/gas state.
So, the first option is to use blue or green lasers (Nuburu specializes in copper welding using blue lasers: Nuburu awarded core patent for blue light copper welding | Industrial Laser Solutions).
The second option is to use high-power infrared lasers, which is a more mature technology. The high power of these lasers, up to 25 kW, compared to 2 kW for green or blue lasers, overcomes the problem of absorption in the solid state and increases process speeds in the keyhole regime.
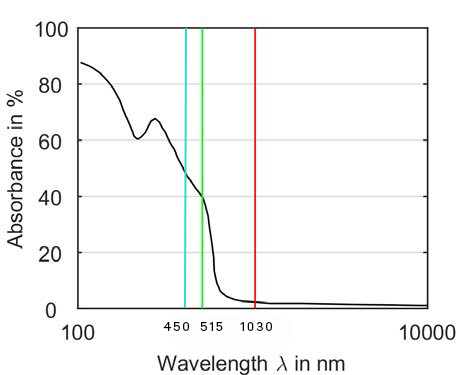
Source : Comparison of different system technologies for continuous-wave laser beam welding of copper (researchgate.net) (pdf)
Laser beam shaping provides a solution to these problems. Cailabs, with its CANUNDA-HP module based on its patented Multi-Plane Light Conversion (MPLC) technology, can optimize the shape of the laser beam to enhance welding performance. CANUNDA-HP has already demonstrated performance at 16 kW, and should even be able to go to 30 kW!
This means that it can manage the high power required for infrared copper welding, and for the extreme thicknesses required in shipbuilding. Furthermore, CANUNDA-HP can provide all types of beam shaping: a ring beam with the standard CANUNDA-HP Ring Shaper, or a customized more intense spot surrounded by a ring, which is ideal for welding copper.
As mentioned above, laser welding can create instabilities leading to the degradation of the quality of the weld bead: porosity, irregular bead, projections, etc. Cailabs is also working on using beam shaping to solve this problem, through various partnerships:
- Cailabs is part of the European Custodian project, a consortium of 10 academic and industrial entities working to develop high power laser machining processes. Through this partnership, the solution developed by Cailabs will result in a 95-98% reduction in welding defects and a 70% reduction in manufacturing time, while reducing costs by 20%.
- Cailabs also collaborated with the Institut Maupertuis, a specialist in laser welding processes. In this project Cailabs demonstrated that, in an industrial application, its technology increases weld quality compared to a normal laser or other technology (dual-core fiber). Using a CANUNDA-HP head to shape a ring resulted in wider, smoother weld beads and less spatter.
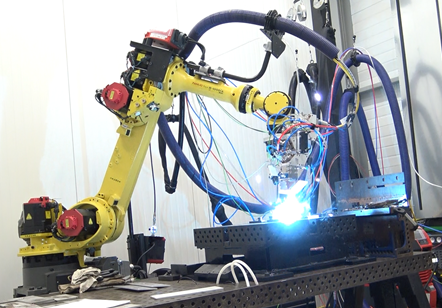
This module provides a ring beam shape, with no focus shift.
The next article in this series will present and compare the different laser beam shaping technologies, still for welding applications.
References :
(1) Seiji Katayama – Fundamentals and Details of Laser Welding, Chapter 10
(2) Trumpf – Laser welding. For more information
(3) EWG – Quels défauts de soudure contrôler visuellement ? Read the article (in French)
(4) Fastener Engineering – How is laser welding used in the automotive industry? Read the article
(5) Industrial Laser Solutions – Will copper welding be the catalyst for laser revenue? Read the article
(6) Institut Maupertuis – Fiche Techno Soudage hybride Laser – MIG/MAG Read the presentation (in French)
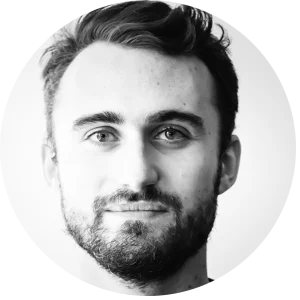
By Julien Bayol
Julien Bayol holds a Master’s degree in mechanics from INSA and has completed a Master’s degree in Management at Toulouse Business School. Very interested in advanced manufacturing techniques, through the use of innovative optical solutions, Julien is assistant product manager at Cailabs. He contributes to the development and commercialization of CANUNDA and TILBA® products.