The challenges of e-mobility: Welding busbars
With the development of e-mobility, the task of welding busbars – connectors allowing electricity flow between various components – has become essential for battery manufacturers. This process is expensive and poorly controlled, making it a major challenge for today’s automotive industry.
Note: This article is the second in a series on lasers in e-mobility
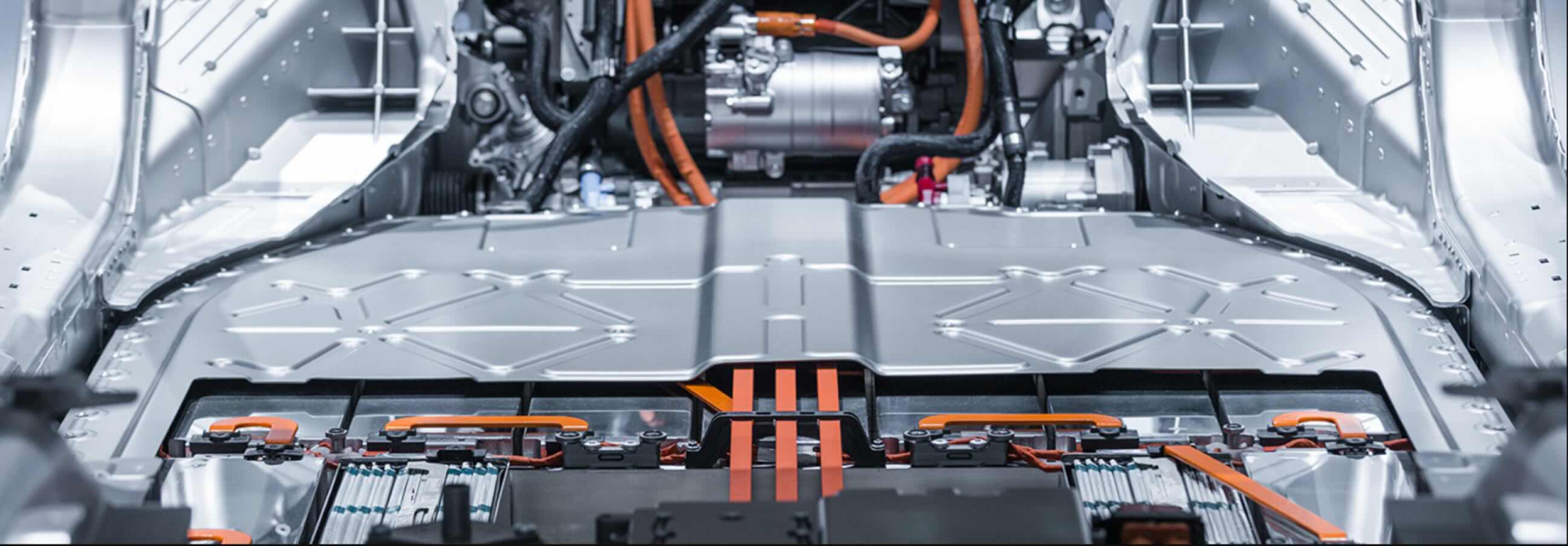
What is a Busbar?
The battery is the heart of an electric vehicle, supplying the energy needed to power the vehicle.
Structurally, a battery is composed of cells. Since a single cell is not sufficient to power a vehicle, multiple cells are welded into packs or modules, which are then assembled into a battery. The assembly can be done in various ways: bolting, screwing, bonding with conductive strips, riveting, or welding.
Busbars are an important component of battery design. These electrical conductors, typically made of copper or aluminum, link the battery cells. Insulated to prevent short circuits, they facilitate the flow of electrical current through the cells and distribute power to the electric motor.
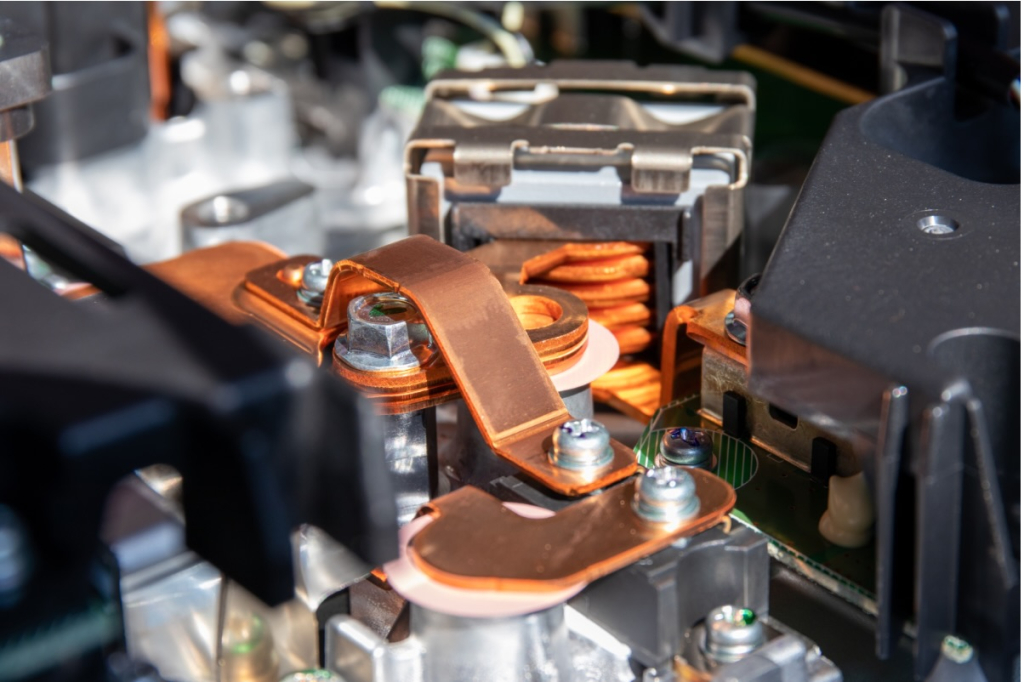
Busbars offer several advantages:
- Size and weight: Since vehicle batteries are already quite heavy, minimizing their weight is essential to improve the car’s performance. Busbars are typically compact and sometimes made of aluminum to further reduce vehicle weight.
- Rigidity: The busbar assembly helps maintain the integrity of the entire structure.
- Flexibility: Copper and aluminum are used for their ability to endure elastic and thermal forces.
- Service and maintenance: The structured layout of busbars enables the quick and safe replacement of components.
- Thermal management: Busbars help reduce heat-generating electrical losses and aid the cooling system.
Busbars come in a variety of shapes, sizes and configurations to meet specific requirements. They can also be wrapped in electrical insulation to improve their safety and reliability.
Welding Busbars:
The surge in e-mobility manufacturing has led to an increased demand for electric batteries and, consequently, for busbars. To enable the electrical current to flow through the battery, busbars must be securely welded to the battery cells. Therefore, one of the biggest challenges is optimizing the welding of these components, a task made complex by the specific properties of the metals involved.
As highlighted in our previous article, laser welding is the most effective technique for the automotive industry. This method produces high-volume, high-quality welds and is particularly well-suited for welding copper and aluminum. These materials are preferred for their stable electrical conductivity over time, even during the strong vibrations typically experienced in a car.
- Copper: Welding copper is challenging due to its high reflectivity at 1 µm – the wavelength of conventional infrared lasers. This means that only about 5% of the laser energy is absorbed at room temperature, making it difficult to initiate the welding process. However, once welding starts, energy absorption increases during the liquid phase. Copper’s high thermal conductivity makes welding unstable, leading to potential defects such as:
- Porosity, which can diminish electrical conductivity.
- Spatter, which can cause short circuits.
- Cracks, which can adversely affect mechanical performance.
- Aluminum: Welding aluminum is also challenging due to its ductility, which can lead to deformation during the welding process. Like copper, aluminum’s high thermal conductivity also makes welding unstable. Certain alloys, such as the Aluminum 6xxx series, are more complex to weld than others.
Due to the high cost of copper, minimizing defective parts is essential. Achieving optimal electrical conductivity and durability in copper welds requires them to be free from pores and spatter, which can only be done through laser beam shaping. Aluminum’s ductility also poses a challenge for achieving high-speed, high-quality welds without beam shaping. Additionally, different EV components require specific welding configurations, including varying weld sizes, depths, and arrangements.
Some industry players are exploring the use of green lasers for copper, because it absorbs 40% of the laser energy at 20°C – eight times more than infrared. However, green laser solutions are currently costly and have power limitations (up to 3kW). As a result, the industry seems to be increasingly looking towards beam shaping solutions for the future.
Cailabs’ solution: Canunda HP
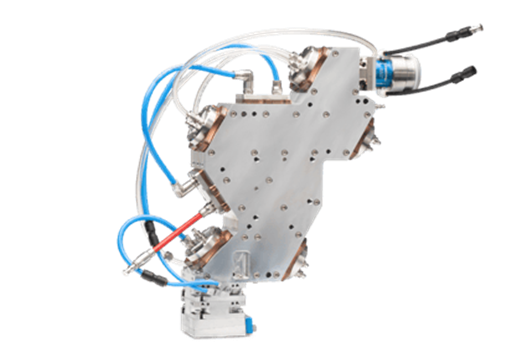
Cailabs’ patented Multi-Plane Light Conversion (MPLC) technology coupled with the CANUNDA-HP laser head optimizes the laser beam shape to improve welding performance. CANUNDA-HP has already demonstrated its capabilities at 16 kW, and the potential for this technology is even more promising, with expectations for its use up to 30 kW and higher!
This makes it possible to handle the high-power demands of copper welding with infrared lasers. CANUNDA-HP can also generate any type of beam profile required: a ring using the standard CANUNDA-HP Ring Shaper, or an intense spot surrounded by a ring, which is particularly effective for copper welding. The key advantage of this solution lies in its ability to focus the energy on targeted areas to optimize the welding process. It is also a cost-effective solution, since the CANUNDA-HP head can be adapted to all types of lasers.
Testing:
Institut Maupertuis:
To demonstrate its efficiency, our MPLC solution was tested on Cu ETP copper samples (100 mm x 50 mm x 10 mm) in collaboration with the Institut Maupertuis. This test compared our solution with a conventional dual-core fiber laser available on the market. For the experiment, we used an 8 kW laser channeled through a 100 µm diameter single-mode fiber fitted with the CANUNDA-HP head. The assembly was mounted on a FANUC R-1000iA/80F 6-axis robot arm. The optical system consisted of collimation and focusing lenses of 200 mm and 250 mm, respectively.
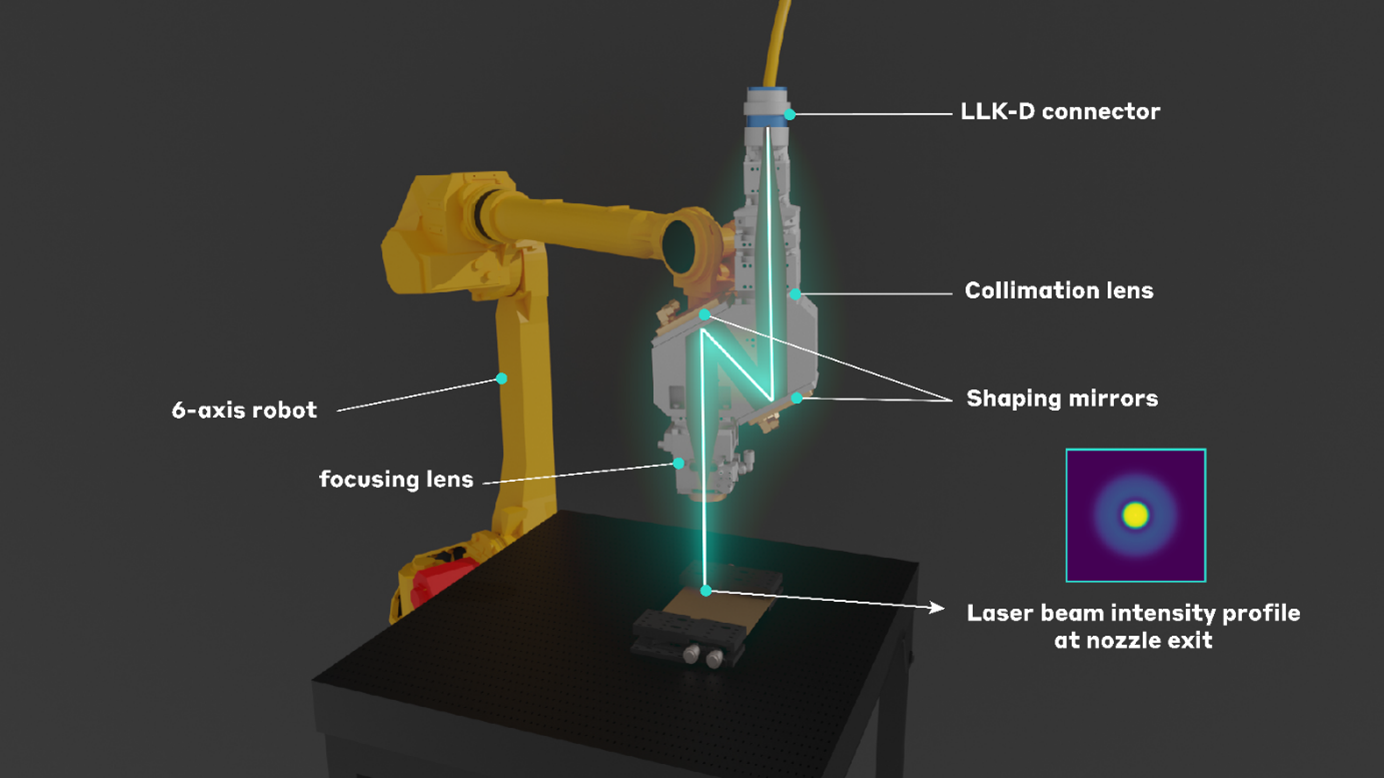
The tests produced an industry-standard weld with minimal pores and spatters at speeds up to 15 m/min. The process window was 1.25 times greater compared to the conventional Brightline dual-core technology.

IFSW:
A second series of tests was conducted in collaboration with IFSW to further characterize weld pool behavior using X-ray imaging. To comprehensively analyze the welding process, an X-ray tube was placed in front of the sample, with a camera set up behind it. This setup facilitated real-time monitoring of key quality parameters, including capillary length, pore formation and spatter.
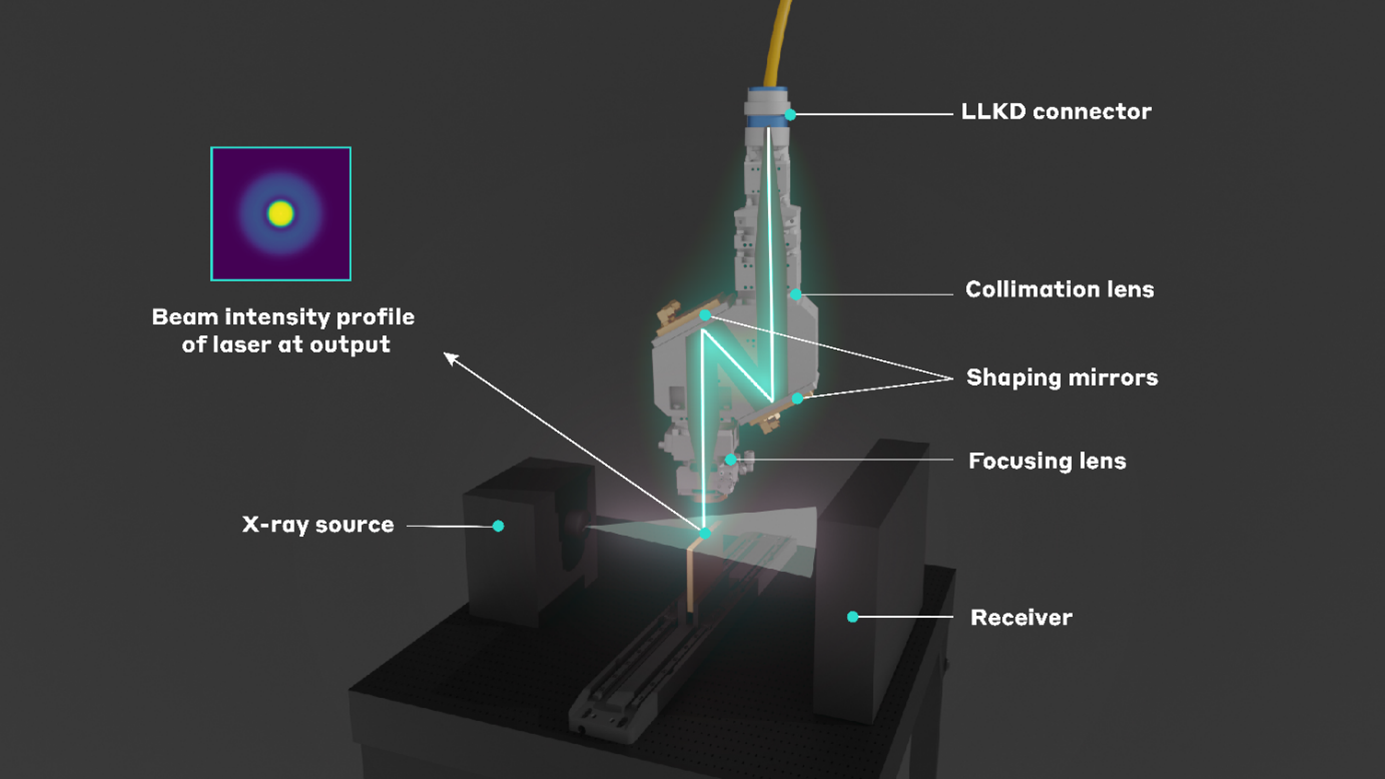
This time, the welds were compliant at speeds of up to 35 m/min (compared to 25 m/min for the dual-core technology). The Cailabs’ solution also preserved its shape up to +/- 4 mm deviation, whereas the dual-core solution began to show deformation beyond a 2 mm deviation.
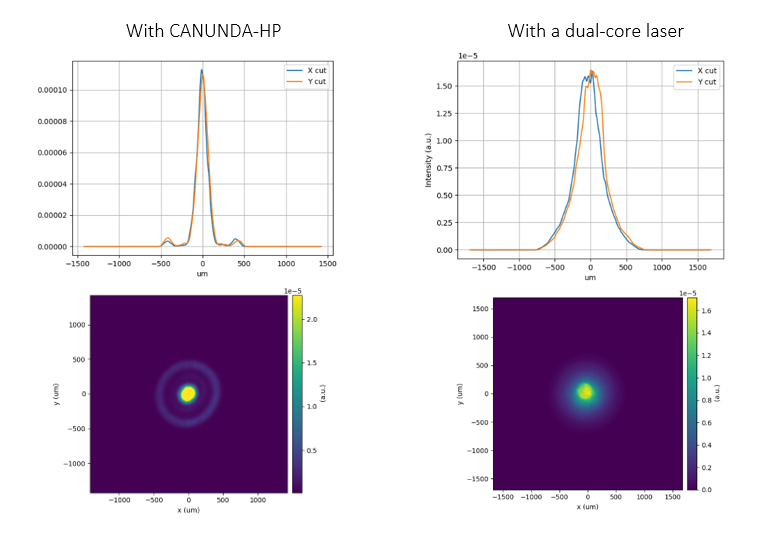
Welding busbars:
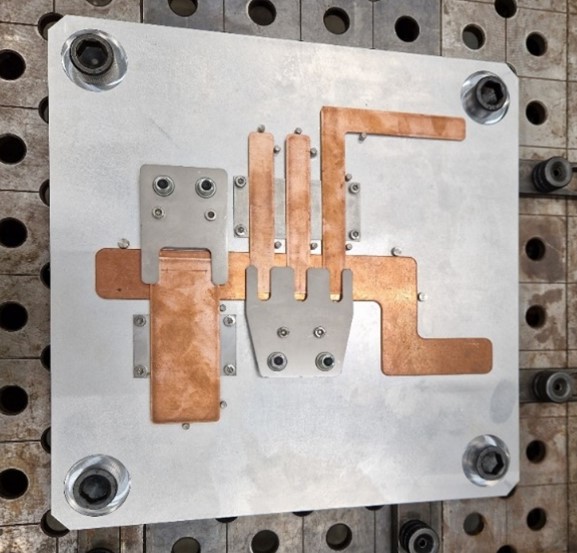
To take our testing even further, we once again collaborated with the Institut Maupertuis, this time welding real Cu ETP copper busbars using our CANUNDA-HP Custom head. The custom head generated a beam with an intense central spot (accounting for 70% of the power) surrounded by a ring, an optimal configuration for copper welding. The setup was similar to the one used during our previous tests at the Institut Maupertuis.
Three 1 mm busbars and a 3 mm busbar were welded to a 2 mm bar. The 1 mm busbars are commonly used in distributing electricity to EV engines, while the 3 mm busbars are more typically used in trucks. The busbars were firmly anchored to prevent moving during the welding process. The 3 mm busbar was welded at a speed of 5 m/min and 8 kW power. Following this, the 1 mm busbars were welded at 6 m/min using 5.5 kW power. In each case, two weld seams were produced for enhanced robustness.
Results:
These tests produced weld beads that met the criteria of ISO standard 13919-2, without any spatter. Cross-sectional macrographic analysis showed an absence of pores.
Configuration 3 on 2mm:

Configuration 1 on 2mm :
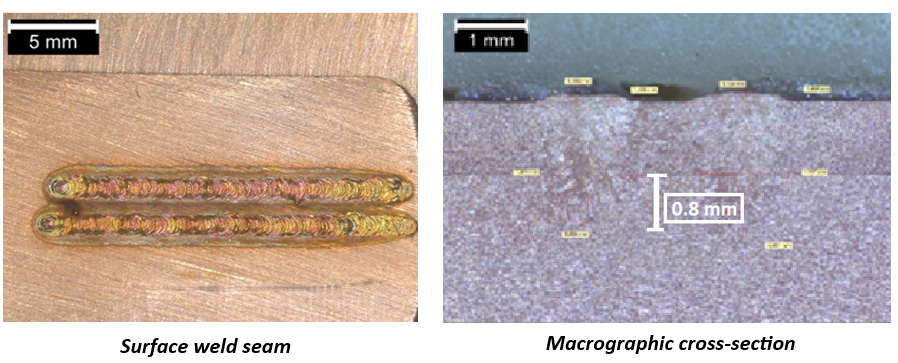
These tests validate the ability of our solution to consistently deliver high-quality welding under industrial conditions.
Marking Cailabs’ 10th anniversary, we conducted a live welding demonstration at the Laser World of Photonics fair in Munich in 2023. Attendees at the event saw a presentation featuring a live broadcast of a busbar being welded at the Institut Maupertuis in France. If you missed this event, you could find the replay here: [LIVE DEMO] Busbars Copper Laser Welding for e-mobility applications.
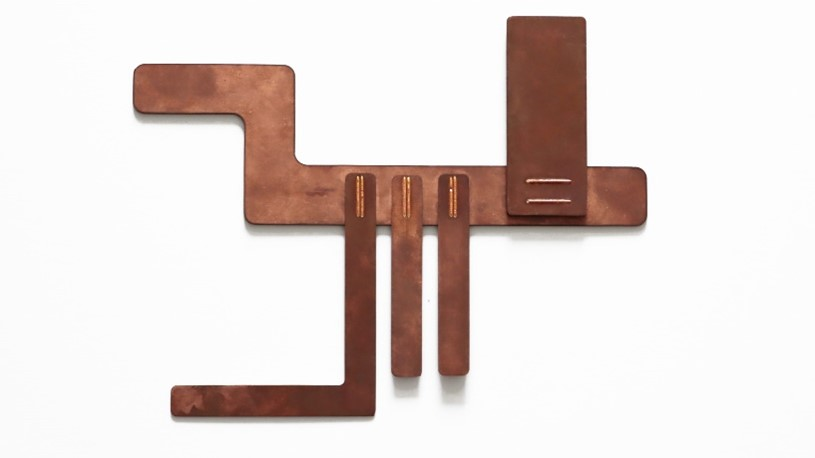
In our upcoming articles, we will explore additional industrial processes that can be improved using products from Cailabs’ CANUNDA range.
References:
(1) What is Busbars and How it benefits EV Battery Modules ? – Prostech. Read the article
(2) Le soudage des alliages de cuivre – Expertise Métallurgique. Read the article
(3) Transport – Les atouts de la soudure laser pour fabriquer des batteries – Laser Magazine. Read the article
(4) Laser Technology in E-Mobility Applications – TRUMPF Laser- Johannes J. Bührle . Read the article
(5) Avantages de laser 520nm VS 532nm ordinaire – LaserPuissant.com. Read the article
(6) Diodes Laser : Principe et Technologie – astuces pratiques . Read the article
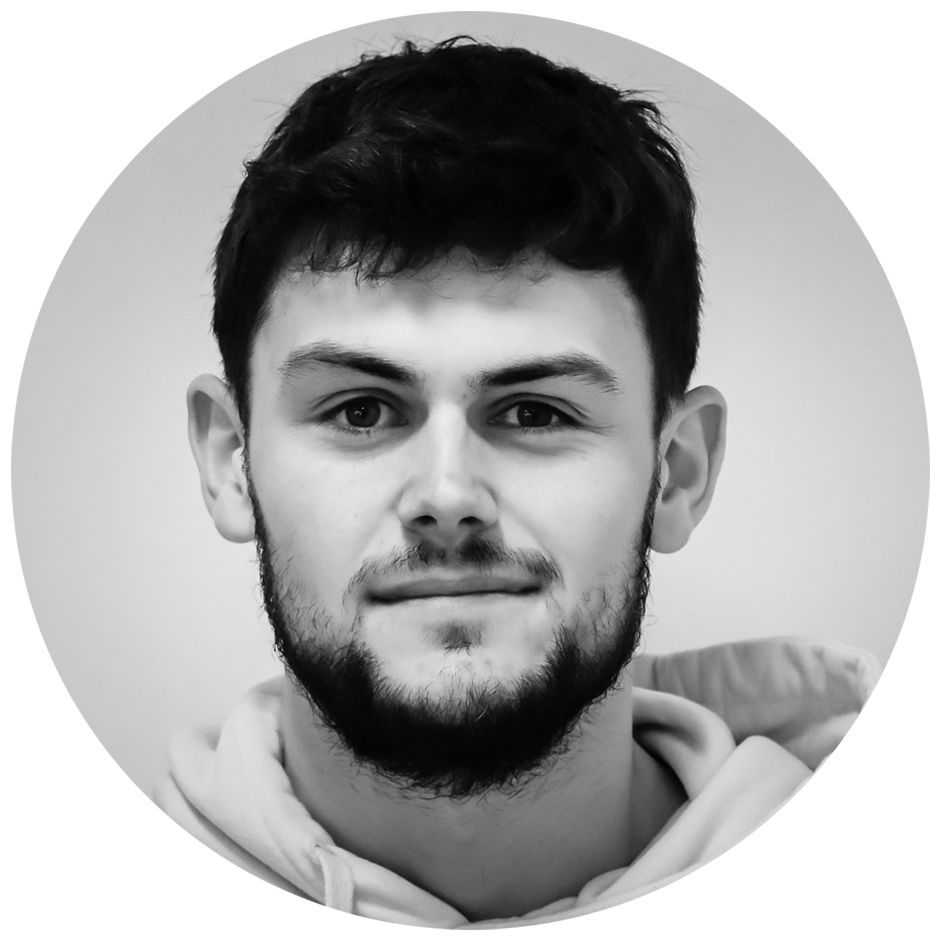
By Adrien Douard
Currently a student engineer specializing in industrial engineering at ECAM Rennes, Adrien Douard completed a year of Operations Management at ESSCA in Angers. Particularly interested in the automotive industry and its processes, Adrien is assistant product manager at Cailabs. He contributes to the development and commercialization of CANUNDA products, that optimize the quality and performance of laser based machining processes.
Our Other Articles:
-
Exceeding Throughput Limits with Laser Communications
-
The challenges of e-mobility: Welding busbars
-
Flying further with beam shaping
-
From the Volkswagen Golf to the Tesla Model 3: How Lasers Are Shaping the Automotive Industry?
-
Space Optical Communications: Why Are Space-to-ground Links Taking Time to Develop?