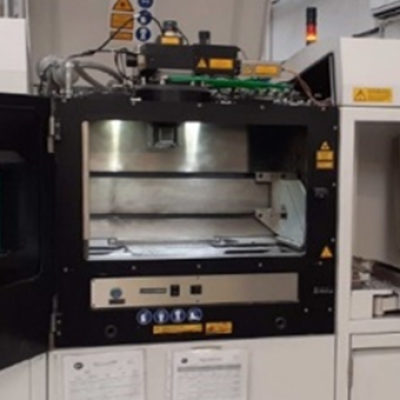
CORIOLIS improves composite fiber placement with CANUNDA-HP Top Hat Shaper
Coriolis, France
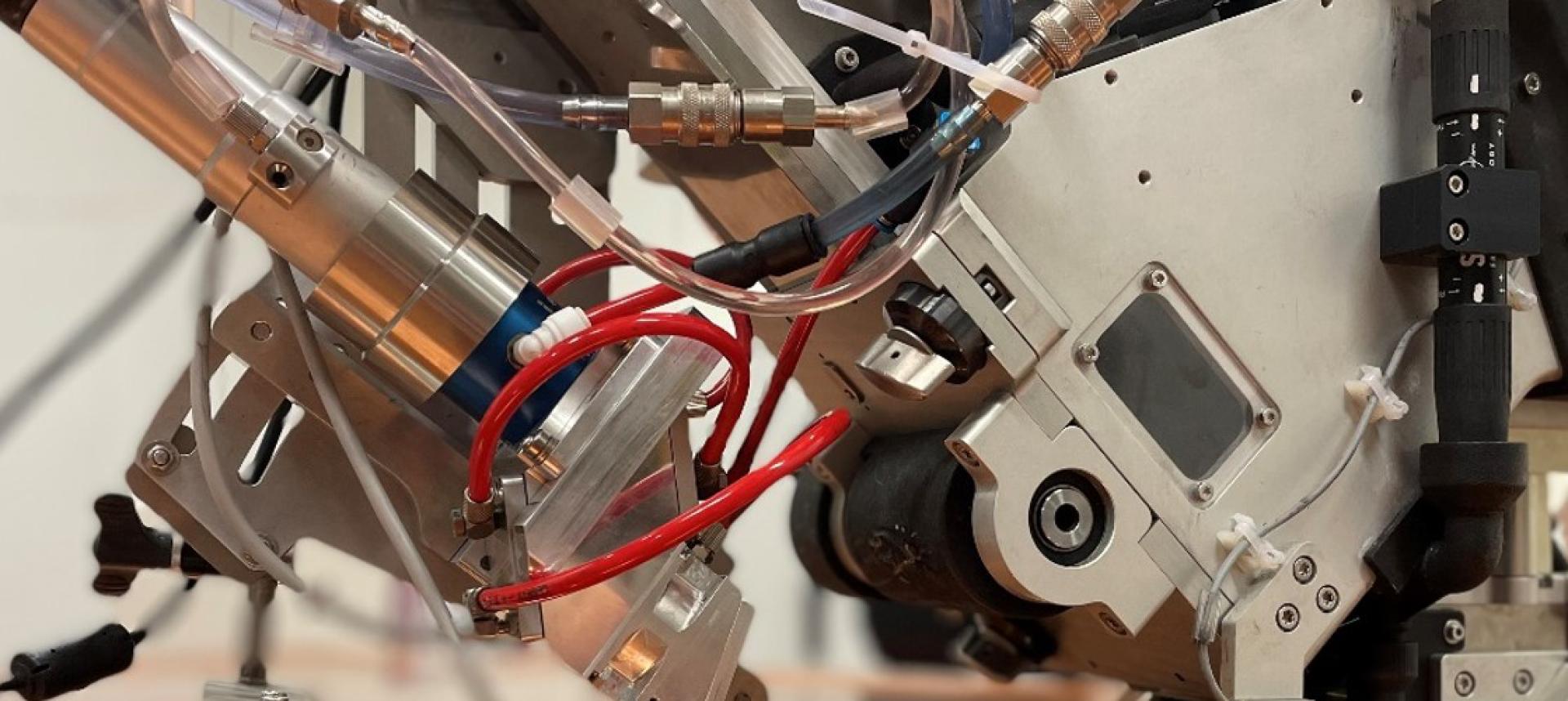
Automated Fiber Placement …
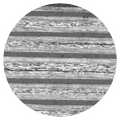
> Thermoplastic fiber placement
> 950-1080 nm
> 6kW
> Footprint: 1kg
> – 40% Porosity
…with a rectangular top-hat
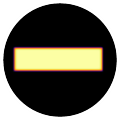
in the processing plane:
> Sharpness: 1/7
> <3% RMS homogeneity
Compacity x2
The partner
CORIOLIS Composites, a French company specializing in automated manufacturing processes for composite materials, produces automated fiber placement robotic systems for the aerospace, automotive, naval and wind power industries.
The application
Composite Automated Fiber Placement (AFP) is an additive manufacturing process in which strips of material are deposited layer-by-layer on a mold. It is primarily used in aeronautics, since composite materials reduce the weight of components while maintaining the same level of mechanical resistance.
The problem
During the process, the heat must be applied in a uniform and targeted manner. The heat source can be an IR lamp for thermoset fiber, or a laser for thermosetting fibers, which requires a higher temperature. Coriolis Composites required an ultra-compact system with a very small dispensing head capable of manufacturing components with complex geometries.
The CANUNDA-HP solution
The CANUNDA-HP Top-Hat Shaper is an ultra-compact continuous-wave laser beam shaper designed to handle high power lasers. Its fully reflective design based on Cailabs’ MPLC technology generates a very homogeneous, sharp intensity profile. Its versatility means that it can be easily installed on different machines
“The solution developed by Cailabs enables us to produce high-quality composite components. The module has a very small footprint, which allows our machines to drape highly curved parts”
Yvan Hardy, Technical Director CORIOLIS Composites
Industrial integration of the CANUNDA-HP Top Hat Shaper
The CANUNDA-HP Top-Hat Shaper head was installed on the C-solo machine developed by Coriolis to perform thermoplastic fiber placement. Its small footprint and light weight of 1kg (including 500g for the laser connector) make it an easily integrated solution. Its water-cooling system enabled a continuous high-power operation.
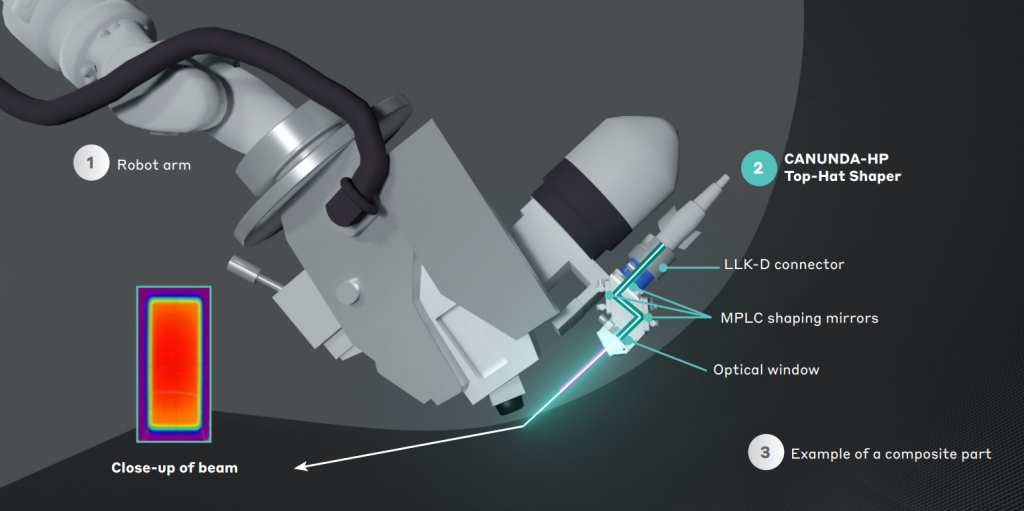
The CANUNDA-HP Top-Hat Shaper laser head generated a rectangular top-hat profile of specific dimensions (confidential data) with homogeneous energy distribution.