Les défis de l’emobilité : le soudage des busbars
Avec le développement de l’e-mobilité, le soudage des busbars, liant les différents éléments entre lesquels l’électricité doit circuler, est devenu indispensable pour les fabricants de batteries. Il s’agit pour le moment d’un processus coûteux et peu maîtrisé. C’est donc l’un des enjeux majeurs dans l’industrie automobile actuelle.
Nb : cet article est le deuxième d’une série consacrée à l’utilisation des lasers dans l’e-mobilité.
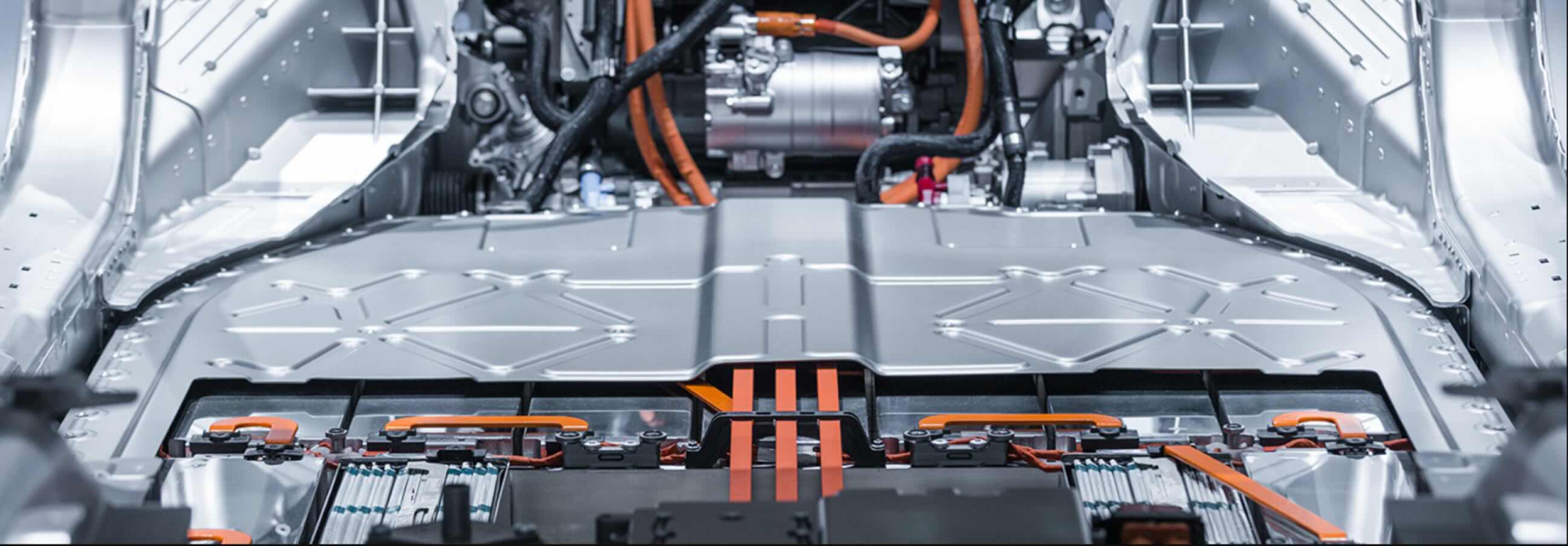
Qu’est-ce qu’un Busbar ?
La batterie est le cœur d’un véhicule électrique, c’est elle qui permet d’alimenter en énergie l’ensemble du véhicule.
Structurellement, chaque batterie est constituée de cellules. Une cellule n’étant pas suffisante pour faire avancer un véhicule, il faut souder plusieurs cellules en packs ou modules, pouvant eux-mêmes être assemblés en nombre pour former une batterie. L’assemblage peut être réalisé par différents moyens : boulonnage, vissage, collage avec des bandes conductrices, rivetage ou soudage.
Les busbars sont des éléments importants dans la conception de ces batteries. Ce sont des éléments conducteurs généralement en cuivre (parfois en aluminium) qui relient les cellules entre elles et qui sont également séparés par un isolant pour éviter les courts-circuits. Ils fournissent une connectivité efficace entre les cellules et permettent le passage de courant électrique à travers elles. Les busbars permettent également d’alimenter le moteur électrique en énergie.
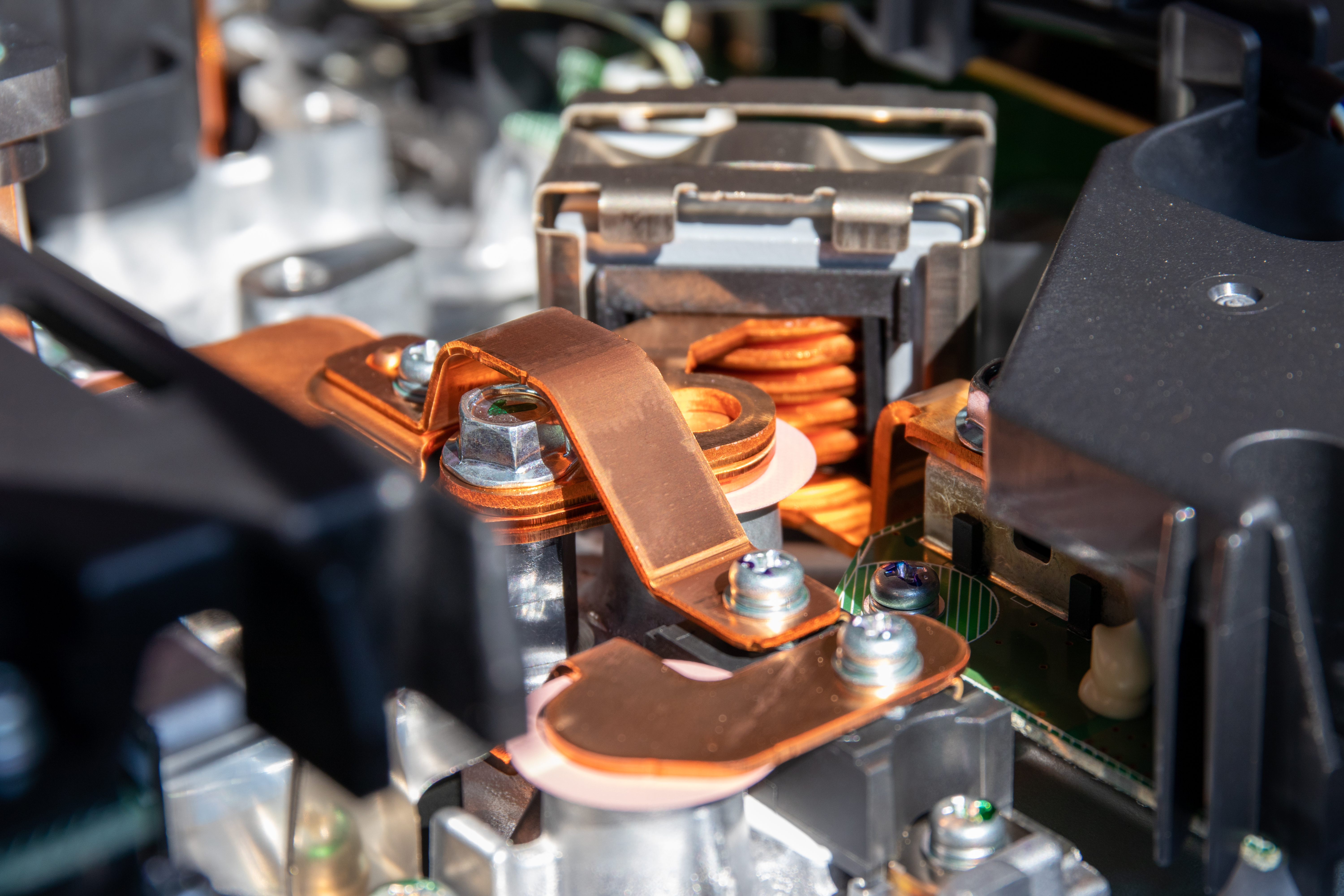
Les busbars possèdent d’autres avantages :
• Taille et poids : Les batteries des véhicules étant déjà très lourdes, il est impératif d’alléger au maximum ces dernières pour améliorer les performances de la voiture. C’est pourquoi, les busbars sont généralement de petites tailles. Ils sont parfois fabriqués en aluminium pour diminuer encore davantage le poids du véhicule.
• Rigidité : L’ensemble des busbars permet de maintenir l’intégrité de l’assemblage.
• Flexibilité : Le cuivre et l’aluminium permettent de faire face aux forces élastiques et thermiques.
• Service et maintenance : Grâce à une organisation structurées, les busbars permettent un remplacement sûr et rapide des composants.
• Gestion Thermique : Réduisent les pertes électriques génératrices de chaleur et assistent le système de refroidissement.
Les busbars peuvent être de différentes formes, tailles et configurations en fonction des besoins et peuvent être enveloppés dans une isolation électrique pour améliorer leur sécurité et leur fiabilité.
Le soudage des Busbars :
Avec la croissance du marché de l’e-mobilité, la demande de batteries électriques et donc de busbars ne cesse d’augmenter. Afin de permettre le passage de l’électricité dans toute la batterie, les busbars doivent être soudés aux cellules. Optimiser la soudure de ces composants est donc un enjeu important. En effet, il s’agit d’un processus difficile en raison des matériaux qui les composent.
Comme expliqué dans notre article précédent, le soudage laser est la technique la plus appropriée dans l’industrie automobile car elle permet d’effectuer des volumes importants tout en gardant un haut niveau de qualité. De plus, le laser est particulièrement apprécié pour le soudage du cuivre et de l’aluminium car c’est une solution qui offre une meilleure stabilité dans le temps en matière de conduction du courant, y compris dans un contexte de fortes vibrations (ce qui est le cas dans une voiture).
• Cuivre : Souder du cuivre est compliqué car le cuivre réfléchit grandement le 1µm (longueur d’onde des lasers traditionnels infrarouges), on a donc peu d’énergie pour initier la soudure. Il absorbe seulement 5% de l’énergie à température ambiante. Une fois initiée, l’absorption du cuivre augmente en phase liquide. De plus, c’est un matériau qui a une bonne conduction thermique ce qui rend sa soudure instable. Certains défauts de soudure peuvent également apparaître :
o Des porosités qui peuvent réduire sa conduction électrique,
o Des projections qui peuvent entrainer des courts-circuits,
o Des cracks qui peuvent affecter négativement les performances mécaniques.
• Aluminium : Souder de l’aluminium est difficile car c’est un matériau très ductile, il va alors se déformer lors du soudage. Sa grande conduction thermique rend également sa soudure instable. Certaines gammes sont plus complexes que d’autres, comme les Aluminium 6xxx.
En raison du coût élevé du cuivre, l’objectif principal est d’éviter les pièces défectueuses. Pour assurer une bonne conduction électrique et la longévité de ces composants, il est crucial d’avoir des soudures en cuivre sans pores ni projections, ce qui ne peut être obtenu que par la mise en forme du faisceau. De même, l’aluminium étant très ductile, il est difficile d’obtenir des soudures de haute qualité et à grande vitesse sans façonnage de faisceau. En outre, les différentes parties des véhicules électriques nécessitent des configurations uniques, telles que des tailles et des profondeurs de soudures différentes, ainsi que diverses configurations de soudages.
Certains acteurs tentent d’utiliser le laser vert car le cuivre absorbe 40% de son énergie à 20°, soit 8 fois plus qu’en infra-rouge. Cependant ce sont des solutions couteuses et peu robustes pour le moment (seulement jusqu’à 3kW). L’avenir semble plutôt s’ouvrir à des solutions de mise en forme de la lumière infrarouge.
La solution apportée par Cailabs : Canunda HP
Cailabs, et sa technologie brevetée de Conversion Multi-Plan de la Lumière (MPLC), propose d’optimiser la forme du faisceau laser pour augmenter les performances de soudage, grâce à la tête laser CANUNDA-HP. CANUNDA-HP a déjà démontré une tenue à 16 kW, et devrait permettre une utilisation jusqu’à 30 kW et au-delà !
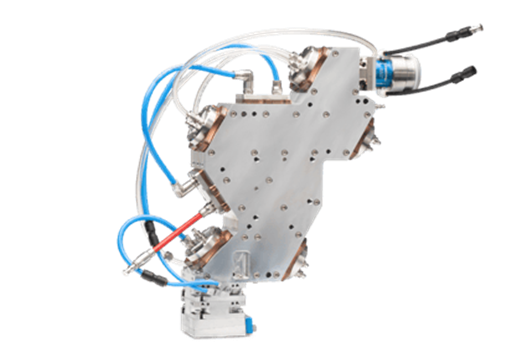
Cela permet justement de gérer les hautes puissances requises pour le soudage du cuivre en infrarouge. De plus, CANUNDA-HP permet de réaliser tous types de mise en forme : un anneau grâce au produit standard CANUNDA-HP Ring Shaper, ou encore un spot plus intense entouré d’un anneau, idéal pour le soudage du cuivre. L’avantage de cette solution est qu’elle permet de concentrer toute l’énergie dans les bonnes zones afin d’optimiser le soudage. C’est également une solution économique puisque la tête CANUNDA-HP peut s’adapter à tous types de laser.
Tests :
Institut Maupertuis :
Pour démontrer sa pertinence, des tests de notre solution MPLC sur des échantillons de cuivre Cu ETP (100mm x 50mm x 10mm) ont été réalisés avec l’institut Maupertuis et ont été comparés à un laser double-coeur classique du marché. Pour cela, nous avons utilisé un laser de 8kW dans une fibre monomode de diamètre 100µm sur lequel on vient placer la tête CANUNDA-HP. L’ensemble est fixé à un bras de robot 6 axes FANUC R-1000iA/80F. Les lentilles de collimation et de focalisation sont respectivement de 200mm et 250mm.
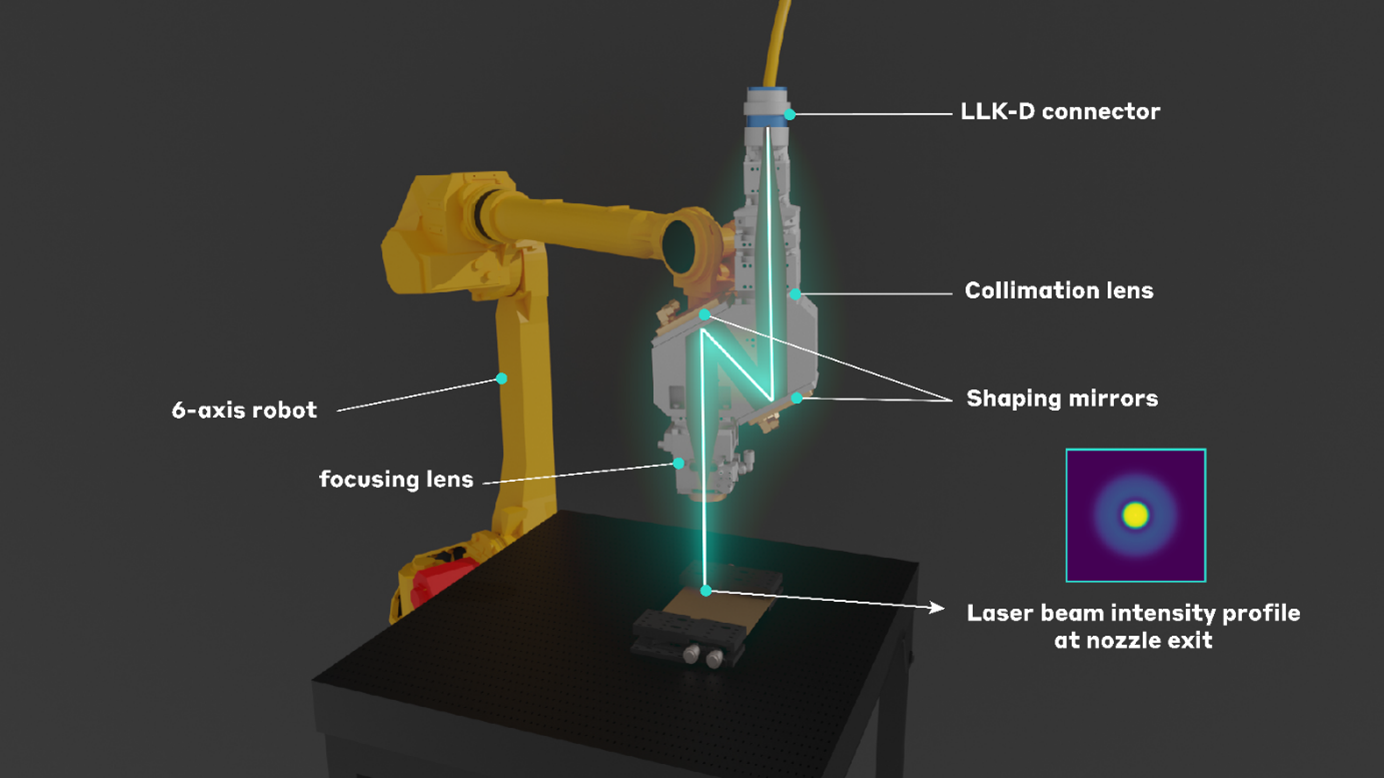
On obtient un soudage conforme aux normes industrielles avec peu de pores et de projections jusqu’à 15m/min. La fenêtre de processus est 1.25 fois supérieure à une technologie brightline double core classique.

IFSW:
Une deuxième série de test a ensuite été réalisée avec IFSW afin de caractériser le bain de fusion par rayon X. Pour avoir un aperçu du processus de soudage, on a placé un tube à rayon X devant, et une caméra derrière l’échantillon. Cela permet de bénéficier d’un suivi de la qualité en direct (longueur capillaire, formation de pores et de projections).
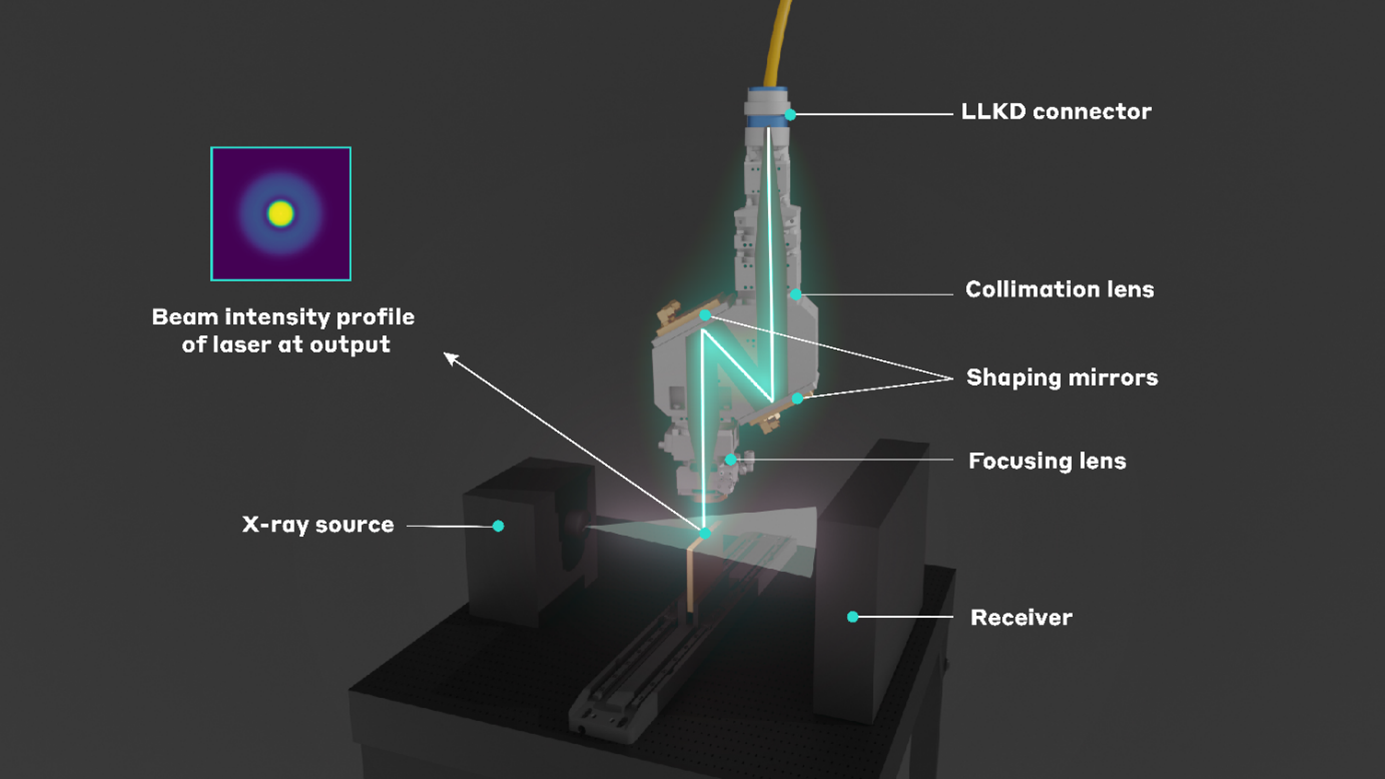
Cette fois, le soudage est conforme jusqu’à 35 m/min (contre 25 m/min pour le double-core). De plus, la solution Cailabs permet de préserver la forme jusqu’à + 4mm alors que celle du double-core commence à se déformer à partir 2mm.
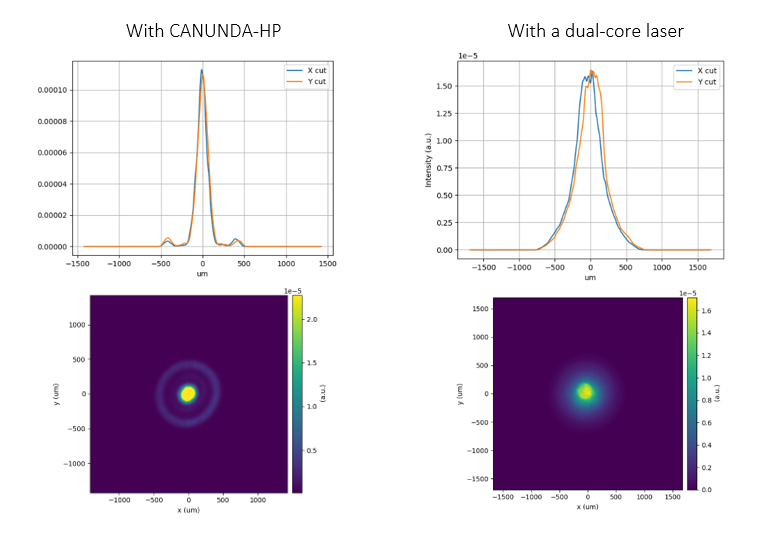
Soudage de busbars:
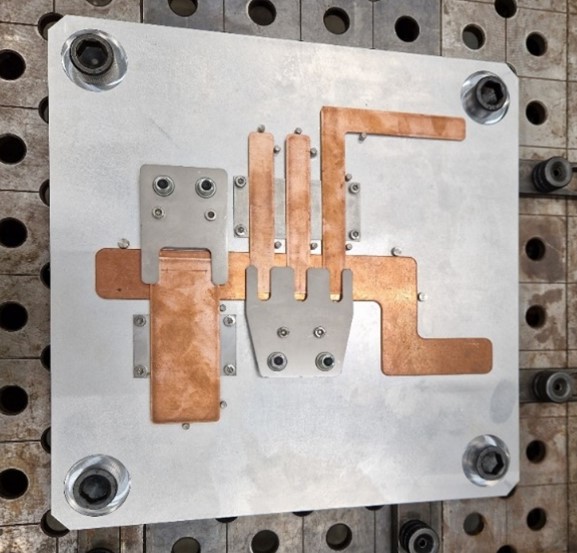
Afin de pousser encore plus loin les tests, nous avons de nouveau fait appel à l’Institut Maupertuis afin de souder de véritables busbars en cuivre Cu ETP à l’aide de notre tête CANUNDA-HP Custom. Cette dernière délivre un faisceau composé d’un spot central intense (70% de la puissance) entouré d’un anneau, idéal pour le soudage du cuivre. Le montage est similaire à celui utilisé lors de nos précédents tests effectués à l’Institut Maupertuis.
On a alors soudé par transparence trois busbars d’1mm d’épaisseur et un busbar de 3mm d’épaisseur, le tout sur une barre de 2mm d’épaisseur. Les busbars d’épaisseur 1mm sont fréquemment utilisés pour le passage de l’électricité vers les moteurs de voiture tandis que ceux de 3mm sont plutôt utilisés dans les camions. Les busbars sont fixés afin d’éviter tout mouvement durant la soudure. Le busbar de 3mm est soudé à une puissance de 8kW à la vitesse de 5m/min. Ensuite, les busbars d’1mm sont soudés à 5.5kW et à 6m/min. A chaque fois on effectue 2 cordons afin d’assurer une plus grande robustesse.
Résultats :
On obtient des cordons conformes à la norme 13919-2 : sans projection. L’analyse en coupe macrographique montre une absence de pores.
Configuration 3 sur 2mm :

Configuration 1 sur 2mm :
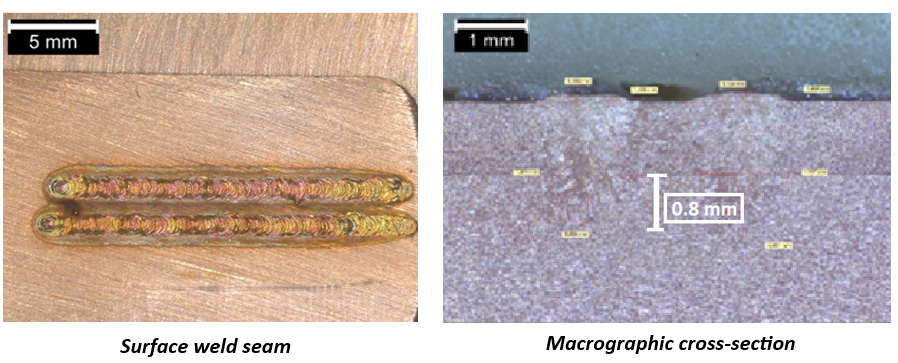
Ces tests permettent de montrer notre capacité à souder du cuivre de manière répétable dans des conditions industrielles et avec un haut niveau de qualité.
En plus de cela, nous avons effectué une démonstration de soudure en live lors du salon World of Photonics de Munich 2023. En effet, pour les 10 ans de Cailabs nous avons organisé un brunch et nous en avons profité pour communiquer sur notre capacité à souder des busbars. Les personnes présentent lors de cet évènement ont alors assisté à une présentation avec une retransmission d’une soudure de busbars en direct de l’Institut Maupertuis en France. Si vous avez manqué cet évènement vous pouvez trouver la rediffusion juste ici : [LIVE DEMO] Busbars Copper Laser Welding for e-mobility applications – YouTube.
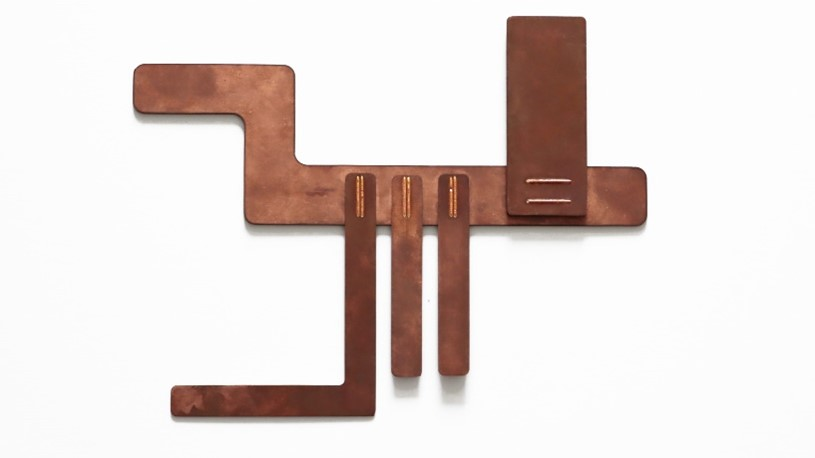
Dans les articles suivants, nous étudierons d’autres procédés industriels qui peuvent être améliorés en utilisant les produits de la gamme CANUNDA de Cailabs.
References:
(1) What is Busbars and How it benefits EV Battery Modules ? – Prostech. Lire l’article
(2) Le soudage des alliages de cuivre – Expertise Métallurgique. Lire l’article
(3) Transport – Les atouts de la soudure laser pour fabriquer des batteries – Laser Magazine. Lire l’article
(4) Laser Technology in E-Mobility Applications – TRUMPF Laser- Johannes J. Bührle . Lire l’article
(5) Avantages de laser 520nm VS 532nm ordinaire – LaserPuissant.com. Lire l’article
(6) Diodes Laser : Principe et Technologie – astuces pratiques . Lire l’article
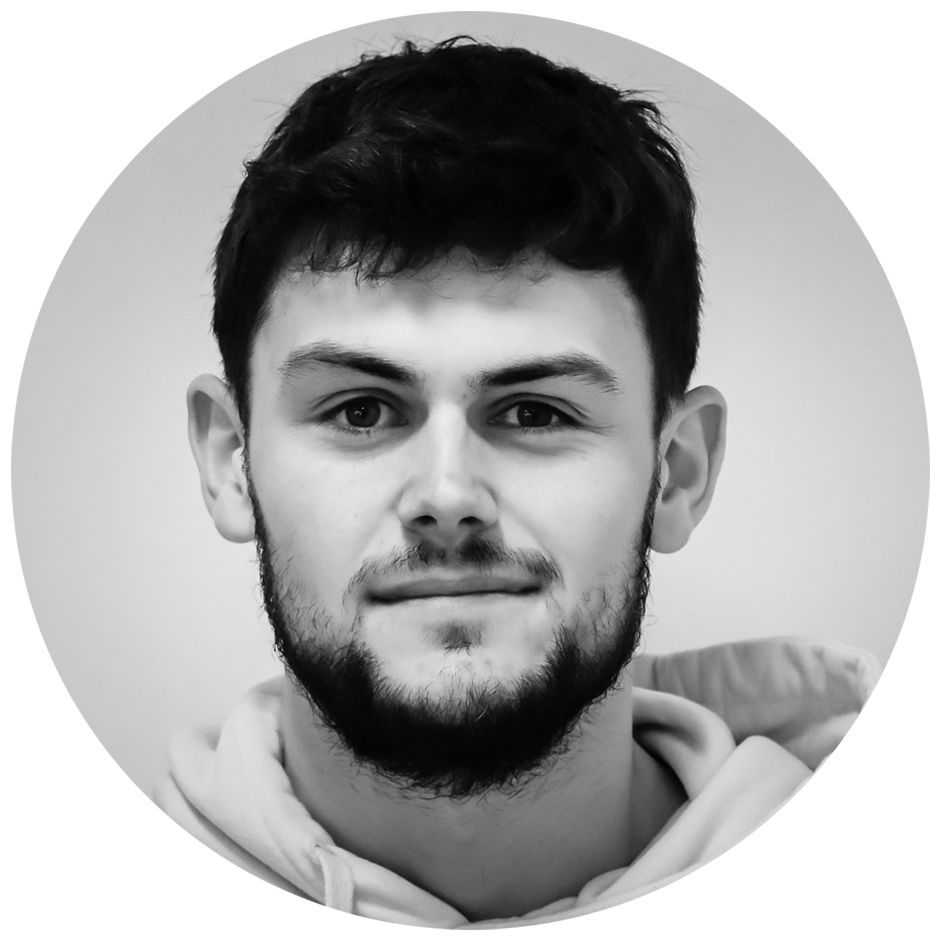
Par Adrien Douard
Actuellement élève ingénieur spécialisé en génie industriel à l’ECAM Rennes, Adrien Douard a effectué une année de Management d’Opération à L’ESSCA d’Angers. Adrien porte un intérêt particulier à l’industrie automobile et ses processus. A Cailabs, Adrien est assistant chef de produit, il contribue au développement et à la commercialisation de la gamme CANUNDA, qui permet d’optimiser la qualité et le rendement des procédés d’usinage laser.
Nos autres articles :
-
Dépasser les limites de débit grâce aux communications laser
-
Les défis de l’emobilité : le soudage des busbars
-
Voler plus loin avec la mise en forme de la lumière
-
De la volkswagen golf à la tesla model 3 : comment les lasers façonnent l’industrie automobile ?
-
Le développement des communications optiques : pourquoi les liens espace terre tardent à se développer ?