Automated Fiber Placement
Managing Complex Geometry with Compact Solution
By using beam shaping we are able to achieve high-quality automated fiber placement (AFP) with a porosity reduced (-40%) compared to gaussian beam. We are also able to manufacture components with very complex geometry by designing more compact (x2) solution.
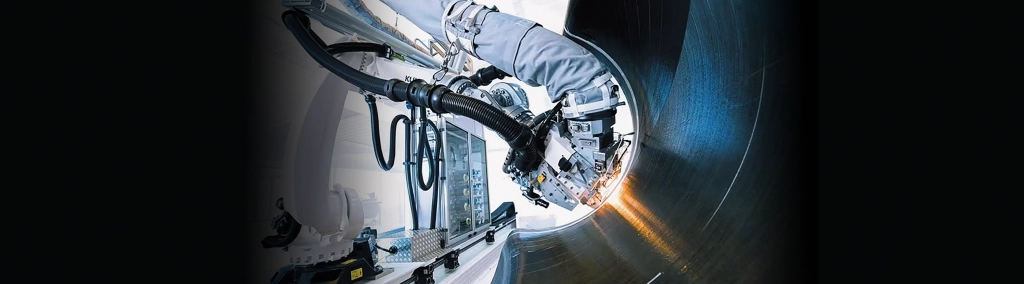
CANUNDA-HP for AFP
Composite Automated Fiber Placement (AFP) represents an advanced additive manufacturing process wherein material strips are meticulously layered onto a mould. This technique is used extensively in the aerospace industry, exploiting composite materials to reduce the weight of components while maintaining their mechanical strength.
The CANUNDA-HP laser head is an ultra-compact continuous laser beam shaper designed to handle high-power applications. It’s very small footprint and light weight of 1kg (including 500g for the laser connector) solution, enabling highly curved parts to be draped. The 1/7 sharpness and the large depth of field (+/- 10 mm) of the rectangular top hat enable to produce high-quality composite components.
However, we also offer customized, flexible solutions to suit a variety of AFP requirements (new beam-shapes, different spot sizes, specific mechanical designs …).
CANUNDA-HP laser heads are used for custom static or dynamic high-power continuous-wave laser beam shaping. Its flexibility and compact design make it easy to integrate on different machines and adapt to various part geometries.
Industrial Integration of CANUNDA-HP
Robot arm
CANUNDA-HP Top-Hat Shaper
LLK-D connector
MPLC shaping mirrors
Example of a composite part
Close-up of beam
An ultra-compact laser head for Automated Fiber Placement
Case Studies
Customize your CANUNDA
Do you want to improve the performance of laser machining processes?
Contact us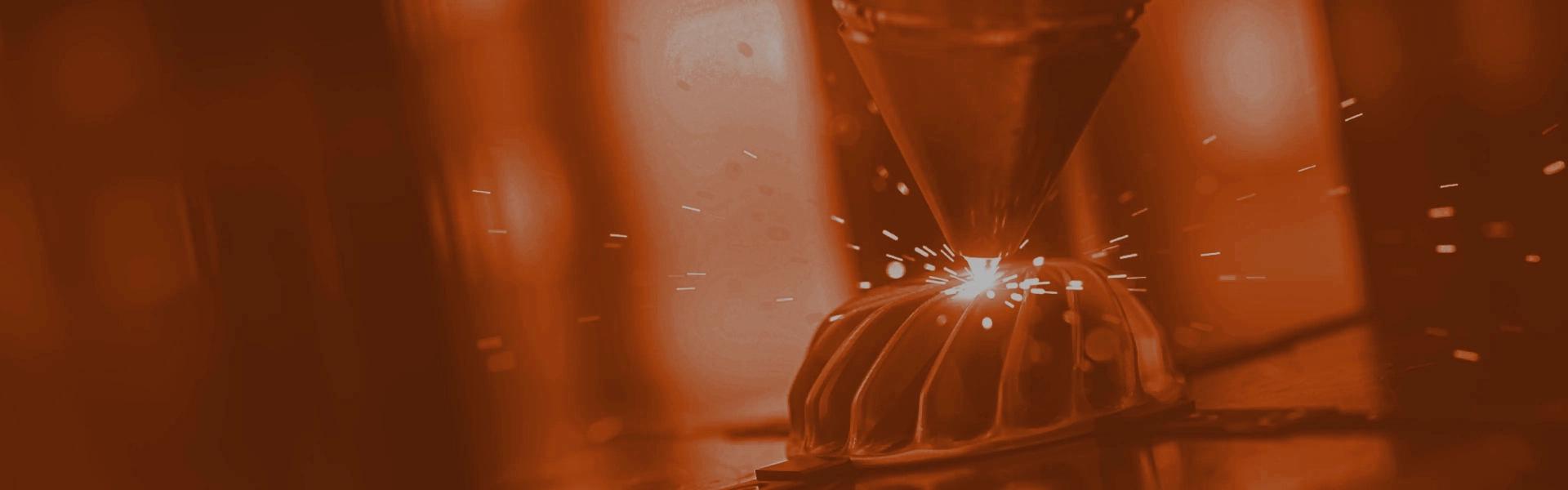